Introduction
As power densities and thermal loads continue to increase in crowded electronic systems, and specific analytical and diagnostic testing processes demand more temperature stabilization for improved accuracy and results, more equipment designers, R&D labs and diagnostic laboratories are turning to liquid cooling solutions for better thermal management. Optimal cooling fluids improve accuracy of results, improve equipment performance, minimize downtime, reduce maintenance costs, ensure safety and can help meet environmental compliance. However, choosing the right coolant for an application depends on many factors such as temperature requirements, heat transfer efficiency, corrosion resistance, material compatibility, environmental considerations, and safety concerns. Water, either purified or deionized, is the most common and efficient coolant used in recirculating cooling systems, making it a standard for comparison to other coolant fluids. Other common coolant types include ethylene glycol, propylene glycol, mineral oil, and dielectric fluids. These coolants differ so significantly that the can greatly influence the design of the cooling system. This article provides an overview into common coolant types and how to select the optimum cooling liquid based on the application.
Coolants and Their Application
Purified Water
In liquid cooling applications, water has an operating temperature range of 0°C to 100°C (32°F to 212°F). Purified water has had chemicals and contaminants removed, but it may still contain minerals. Distilled water is a type of purified water, that has had both contaminants and minerals removed. While some impurities are to be avoided due to potential corrosive effects, completely pure water, like highly distilled water, is hungry for ions and will strip electrons from the metals in a cooling system making it very aggressive and damaging. Highly distilled water should not be used in recirculating chiller applications.
The quality of street (mains) water depends on its storage, delivery, and ultimate source (ground versus surface water). It may contain corrosive impurities, such as chloride, alkaline carbonate salts, or suspended solids. Impure water is also an electrolytic bridge to enable galvanic corrosion if the system possesses dissimilar metals.
Water as a coolant in a recirculating system is also susceptible to biological fouling. Algae, bacteria, or fungi are likely to form depending on the system’s exposure to light and heat and the availability of nutrients in the wetted components. The resultant slime or biofilm can inhibit heat transfer between the fluid and wetted surfaces. In addition to inhibiting heat transfers, biofilm can also cause leaks in mechanical seals used for mating pumps to motors. Sufficient concentration of an additive agent must be considered. For instance, glycol as an additive is commonly used as a control against biological growth, but concentrations less than 20%, the effectiveness is limited; in fact, below 1%, propylene glycol and ethylene glycol act as a bacterial nutrient.
Purified Water
Pros: | Cons: |
---|---|
|
|
Deionized Water
Deionized water (DI) has had its ions removed including sodium, calcium, iron, copper, chloride, and bromide. The deionization process utilizes a resin bed filter to remove these ions and other impurities that can cause corrosion or scale formation. DI is a specialized cooling liquid used in various applications including medium and high voltage systems, particularly in situations when maintaining high purity and preventing ion-induced corrosion is crucial. DI water is versatile and can be used in electronics cooling, industrial processes, laboratory equipment, and more.
Deionized water is an excellent electrical insulator, as it has very low levels of mineral ions to contribute to the electrical conductance of the water.
Even with precautions taken to ensure passivated wetted surfaces through the coolant loop, ionic impurities will develop in the water over time. It is the nature of water to absorb ions from minerals that it contacts, and deionized water, with its lack of ion content, is hungry for them, and aggressively acquires them from contact surfaces.
To keep the original dielectric properties of the water, it must be continuously passed through resin beds. These beds will slowly lose their effectiveness, and regeneration of the bed will have to be performed if the bed is not to be periodically replaced. Complex systems are required for regeneration of mixed beds, and it requires different regenerative agents for the anion (positively charged) and cation (negatively charged) resins. Oils, silt, or metal particles (either from machining operations or precipitates from chemical action such as iron fouling) will also decrease the lifetime of the resin bed.
Deionized Water
Pros: | Cons: |
---|---|
|
|
Glycol-Water Mixtures
There are several complex and interrelated factors to consider when selecting different types of glycol-water mixtures. Ethylene glycol (EG) (typically used in combustion engine cooling) and propylene glycol (PG) are the two most used glycols in these mixtures. Also referred to as coolant or antifreeze solutions, they are organic compounds known for their ability to lower the freezing point of water and increase its boiling point. With an operating temperature range of approximately -50°C to 150°C (-58°F to 302°F), glycol-water mixtures are useful in both cold and hot environments. Ethylene glycol is more commonly used, but is toxic to humans and animals, while propylene glycol is less toxic and is used in applications where safety is a concern, such as in food and pharmaceutical industries.
Propylene glycol also has a higher specific heat than ethylene glycol. However, its thermal conductivity is lower, and its viscosity is higher than ethylene glycol. This results in better overall performance for EG versus PG. In most cases, a mixture of the glycol and water is used with a lower concentration of glycol due to the superior performance of water over either glycol type. EG requires lower concentrations than PG for equivalent freezing point depression, boiling point elevation, and burst temperature depression.
Copper and copper nickel alloys have good resistance against corrosion and a natural resistance to biological growth. As with aluminum, corrosion inhibitors should be employed to avoid acidic corrosion.
The specific concentration of glycol in the mixture depends on the desired freeze protection and heat transfer properties. Higher concentrations of glycol provide better freeze protection but reduce the heat transfer efficiency of the mixture.
It's important to note that handling and disposing of glycol-water mixtures require proper care and attention to environmental and safety regulations due to the potential toxicity of glycols. Manufacturers often provide guidelines and safety information for their products.
Water with Ethylene Glycol
Pros: | Cons: |
---|---|
|
|
Water with Propylene Glycol
Pros: | Cons: |
---|---|
|
|
Synthetic Mineral Oils
Heat exchangers with oil cooling systems are designed to circulate transformer oil and are used in applications where the temperature at the heat source exceeds the operational temperature limit of water-based coolants or when special insulating properties are required within the coolant loop. Mineral oil cooling is a submersion cooling method that delivers uniform cooling to all components immersed in the oil. The non-conductive and non-corrosive synthetic mineral oils are designed specifically for use in cooling applications and offer efficient and safe cooling. With a typical operating temperature range of -40°C to 290°C (-40°F to 554°F), thermally stable synthetic mineral oils offer low reactivity and evaporate over a long period of time. This makes it ideal for adding to submersion cooling systems. Mineral oil cooling is odorless, non-toxic and offers significant noise reduction compared to other liquid or air cooling systems.
However, implementing mineral oil cooling is a complex and messy process. Building a custom enclosure and ensuring a watertight seal can be challenging. In addition, mineral oil can become contaminated with dust and other particles over time, necessitating periodic cleaning and maintenance. Not all components are suitable for submersion cooling. Components like copper and some elastomers cannot be submerged and should be avoided.
Mineral Oil
Pros: | Cons: |
---|---|
|
|
Dielectric Fluids
Used as electrical insulators in high voltage applications like transformers, capacitors, high voltage cables and switchgear, and in immersion cooling applications, dielectric fluids come in various formulations, including synthetic oils and fluorinated liquids, to meet specific application requirements. With a typical operating temperature range of -40°C to 105°C (-40°F to 221°F) or higher, dielectric fluids are chosen based on their dielectric strength, thermal conductivity, and chemical stability. Dielectric fluids, like Shell Diala S4, XG Galden or Fluorinert, enable full immersion of electronics and function to provide electrical insulation, suppress corona and arcing and serve as a coolant
These engineered non-conductive fluids have high chemical stability and are less conductive than water. The fluids are designed to provide electrical insulation and cooling in electrical transformers and equipment where arcing from high voltages to ground or other surfaces is a concern. Similarly, dielectric fluids are used in X-ray tube cooling that requires no electrical conductivity of the fluid driven by voltages in the tens of kilovolts.
These organic fluids often have higher viscosities than water, so it is useful to get supplier data for a pump’s flow and pressure characteristics when operating at the desired fluid’s viscosity.
While dielectric fluids offer advantages in terms of electrical insulation and efficient heat dissipation, they also come with several potential negatives, including complexity, maintenance challenges, cost, and environmental concerns. The decision to use dielectric fluids for cooling should be based on a careful assessment of the specific requirements and trade-offs for the intended application.
Dielectric Fluids
Pros: | Cons: |
---|---|
|
|
Fluid Performance
There are a few thermophysical properties to consider when assessing the thermal performance of a fluid, including thermal conductivity, specific heat, fluid density, and viscosity. The goal for optimizing the performance of these properties is improved heat transfer between the fluid and the heat exchange surfaces it is contacting. Assessing the heat transfer coefficient directly in these cases requires use of correlations developed to calculate the coefficient for various specific geometrical conditions.
Thermal Conductivity – measures how efficiently a fluid can transfer thermal energy through conduction indicating how well a fluid can conduct heat from a higher temperature region to a lower temperature region. It is expressed in the number of Watts per meter thickness of the material, per degree of temperature difference between one side and the other (W/mK). High thermal conductivity equates to high heat transfer, meaning the fluid will heat or cool quicker than one with low thermal conductivity.
Specific Heat – amount of energy needed to raise the temperature of 1 gram of a substance 1 degree Celsius (°C). The units of specific heat are normally calories or joules per gram per Celsius degree. Water is commonly used as a cooling liquid because it has a high specific heat of 4.186 J/g-K. In other words, water can absorb more energy per degree change compared to other substances.
Fluid Density – the measure of spaces between two particles in a given fluid. Data is given in mass per unit volume (kg/m3). Density is important as most heat transfer fluids are thought of in terms of volume (e.g. flow rates) and higher density fluids will have higher mass and generally a better ability to absorb heat (specific heat is dependent on mass).
Viscosity – the measurement of a fluid’s internal resistance to flow, often related to the thickness or thinness of the fluid. Viscosity is usually measured in centipoise (CPS) or poise (100 Centipose = 1 poise). Water, for example, has a viscosity of 1 cP at 70°F / 21°C while an oil such as Shell Diala S4 has a viscosity over 7 cP.
Heat Transfer Coefficient – measures the rate heat is transferred from one medium to another through conduction, convection or radiation. Water has a heat transfer coefficient, or U-value, of about 1000 W/(m2 °C) [176 Btu/(hr-ft2°F)].
Fluid Performance
Fluid | Thermal conductivity (W/mK) | Specific heat (J/kgK) | Viscosity (cP) | Density (kg/m3) | Cost | Boiling point (°C) | Freezing point (°C) |
---|---|---|---|---|---|---|---|
Water | 0.580 | 4186 | 1.00 | 1000 | $ | 100 | 0 |
De-ionized Water | 0.606 | 4200 | 1.00 | 997 | $+ | 100 | 0 |
50-50 Water / Ethylene Glycol | 0.402 | 3283 | 2.51 | 1082 | $$ | 107 | -37 |
50-50 Water / Propylene Glycol | 0.357 | 3559 | 5.20 | 1041 | $$ | 106 | -45 |
Dynalene HC30 | 0.519 | 3100 | 3.70 | 1275 | $$$ | 112 | -40 |
Galden HT200 | 0.065 | 963 | 4.30 | 1790 | $$$ | 200 | -85* |
Fluorinert FC72 | 0.057 | 1100 | 0.64 | 1680 | $$$ | 56 | -90* |
Shell Diala S4 | 0.142 | 2150 | 7.57 | 805 | $$$ | >280 | -40 |
Mineral Oil | 0.136 | 1700 to 2100 | 10 to 1000+ | 870 | $$$ | 218 to 643 | -40 |
Material Compatibility
Stainless steel, and in particular 300 series stainless (austenitic stainless steel), is inert against nearly all heat transfer fluids due to the nature of the chromium (III) oxide passivation layer covering the surfaces of such steels. When using deionized water, stainless and nickel are appropriate for wetted surfaces. Although stainless steel is excellent for use against corrosion in most cases, there is a penalty for using it in the form of a rather low thermal conductivity when compared to other metals such as aluminum or copper.
Aluminum and its alloys have good thermal conductivities, ranging from 160-210 W/mK. However, aluminum tends to be susceptible to corrosion or pitting from impurities in unpurified water. Even with a glycol solution in distilled water, both EG and PG form acidic compounds under oxidation in aluminum. This can cause corrosion to wetted surfaces and the formation of organic acid byproducts. Prevention methods include the addition of corrosion inhibitors to the fluid, or applying surface treatments to the wetted surfaces, such as anodizing aluminum.
Copper and copper nickel alloys have good resistance against corrosion and a natural resistance to biological growth. As with aluminum, corrosion inhibitors should be employed to avoid acidic corrosion.
SWetted surfaces on the pump, including the seals, must be compatible with both the fluid and the expected operating conditions. Galvanic corrosion in systems using different wetted metals can create additional issues including pump seal failure and leaking of toxic fluids.
Cost Considerations
Tap water is the most readily available and lowest cost option, and purified water will be costlier depending on the purity type and level required.
The costs of maintenance associated with a particular type of coolant can be worth noting. This would include filtration, ionization beds, cathodic protection, and top-off from evaporated or leaked fluid. Disposal is another factor – tap or purified water can typically be disposed of in regular drainage, but water mixed with alcohols, other organics, or any organic fluid at all will normally require other disposal methods. Coolants that require periodic flushing and recharging during their lifetime, as well as solutions that must be handled at the end of a system’s life, may have disposal costs that exceed the initial cost of the coolant.
Over time, in an imperfectly closed system (leaks in the seams or seals), the fluid levels can be expected to decrease. Addition of a water/coolant mix to top off fluid levels should involve specifically controlled concentrations of coolant to match the existing system fluid. However, glycols can break down over time into organic acids – measurement of system fluid pH and detection of solid and biological contamination can indicate that changing the coolant solution is required.
Conclusion
There are many types of cooling fluids available to satisfy application requirements. Selecting the right coolant for an application requires an understanding of the characteristics and thermophysical properties of the fluid, including performance, compatibility, and maintenance factors. Ideally, the coolant fluid would be an inexpensive and nontoxic liquid with exceptional thermophysical properties and a long operating life. Each coolant option exhibits different properties, such as thermal conductivity, specific heat, and thermal stability, along with specific advantages, but their usage will ultimately depend on their reliability and economics.
Contact Laird Thermal Systems
Have a question or need more information about Laird Thermal Systems? Please contact us
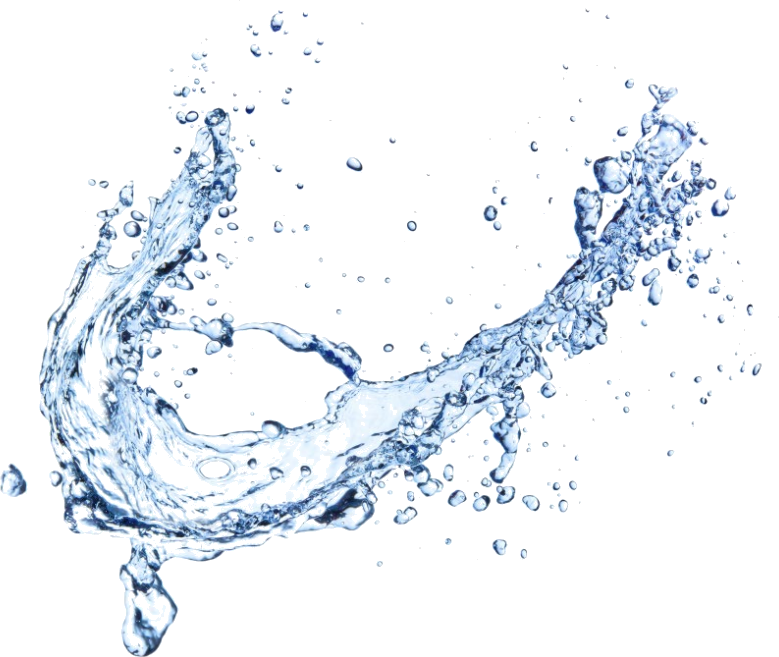