Introduction
Engineers of all disciplines more frequently need a Thermal Wizard, someone who can solve their heat dissipation or critical thermal management problems. If you need a Thermal Wizard or you are that Thermal Wizard that coworkers count on, then you are familiar with the more common issues associated with solving unanticipated or sudden thermal management problems.
1. Selecting the right thermal management product to meet specified or unknown Qc requirements.
2. Developing trial designs to solve what-if scenarios.
3. Choosing the optimum level of complexity and knowing when to engage a thermal solutions vendor.
4. Prototyping custom configurations when standard product performance falls short.
5. Where to find the right thermal management products quickly to meet tight development schedules.
Typically, thermal design follows electrical design, creating potential design issues if product dimensions constrain heat dissipation or an insufficient power supply is allocated to maintain safe operating temperatures. Savvy engineers use past experience, basic thermal calculations, and/or downloaded software tools, such as Laird’s AZTEC™, to answer these thermal questions. Unfortunately, you may not have a past design to rely on or the time to hand-calculate all of the design variations, or the security permissions to install downloaded software from the internet.
Laird Thermal Systems Wizard
Laird Thermal Systems developed the Thermal Wizard to solve all of these issues
The Thermal Wizard is a web-based solution, which links product search to thermal calculators to product availability. This means it is available on any web browser and on any computing platform (PC, Mac, Iphone, Android) running a web browser. Thermal Wizard requires only two specifications, Qc (Cooling Power) and ΔT (Temperature Change) to begin the selection process (See Figure 1).
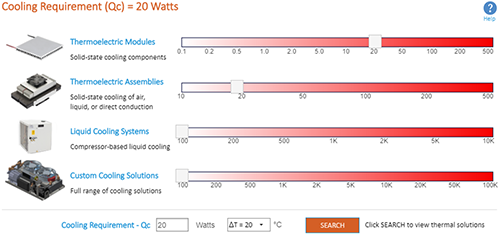
Figure 1: Selecting Qc and ΔT for Thermal Wizard Product Search
If you know these specifications, the main Thermal Wizard product search quickly displays the available Thermoelectric Cooler, Thermoelectric Cooler Assembly or Liquid Cooling System thermal solutions, ranging from a few tenths of a watt to more than five kilowatts. If Qc and ΔT have not yet been determined, Thermal Wizard provides four calculators (Device Cooling, Enclosure Cooling, Air Cooling, Liquid Cooling), each with three preprogrammed examples to quickly get your design underway.
Selecting the right product to meet specifications
The Thermal Wizard product search function uses only two specifications to start the selection process: Cooling Requirement (Qc) and Temperature Change (ΔT). A sliding power bar for each product category type (Module, Assembly or Liquid Cooling System) shows the effective range of Qc.
For example, an optical transceiver design requires a 7 Watts, 940nm multi-mode laser with operating voltage/current of 2.2V/9A for a power supply of 19.8W. The laser needs below ambient cooling to maintain a 25°C package temperature (Tc = 25°C) in an ambient temperature of up to 45°C (Ta = 45 °C). The wavelength drift is 0.3 nm/°C, so maintaining a constant temperature is critical. If we assume minimal environmental heat load and use Qc = 20W and ΔT = 20°C (ΔT = Ta – Tc), this yields a number of possible Thermoelectric Cooler solutions, as well as Thermoelectric Cooler Assembly solutions. All are valid thermal solutions. You can choose one of the thermoelectric cooler solutions and configure with your own heatsink/fan combination or select one of the Thermoelectric Cold Plate (Direct-to-Air) solutions for a higher level of integration and guaranteed performance. If you choose the thermoelectric cooler path, selecting the CP2-31-06-L1-W4.5 will dissipate from 0 to 24 watts with an operating voltage ranging from 0 to 4 Volts (see Figures 2 and 3).
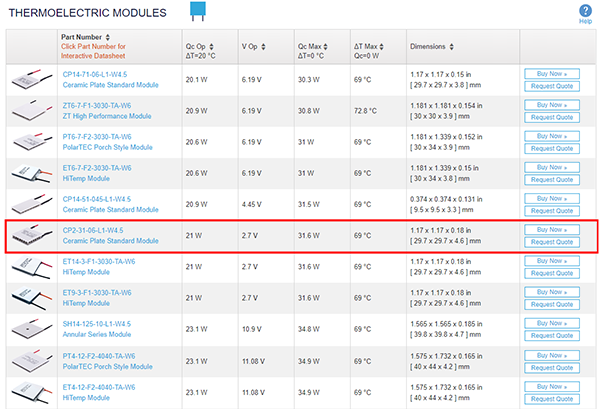
Figure 2: Thermoelectric Cooler Thermal Solutions
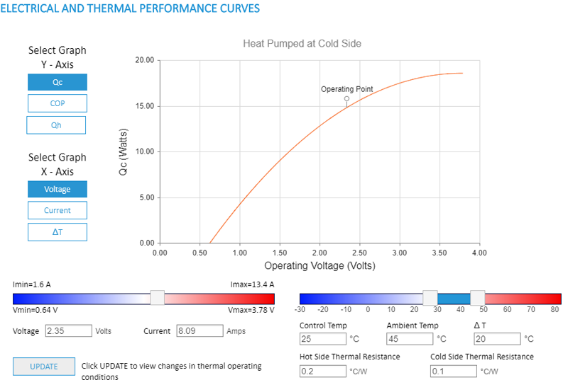
Figure 3: CP2-31-06-L1-W4.5 Qc vs Voltage
Also reversing polarity will reverse the hot and cold sides of the thermoelectric cooler to heat the laser with as much as 76 watts (Qh). This performance assumes no thermal resistance with the hot side not exceeding 45°C. If the thermoelectric cooler must also handle the ΔT of the heatsink, enter those values on the active datasheet to derate the Qc. For example, using a hot side thermal resistance (Θsa = 0.2 °C/W) and a cold side thermal resistance (Θsc = 0.1 °C/W) reduces the maximum Qc to 18.5W.
If you take the thermoelectric cold plate path, selecting the DAT-040-12-02 will provide 0 to 28 watts of cooling over a voltage range of 5 to 20V (see Figures 4 and 5).
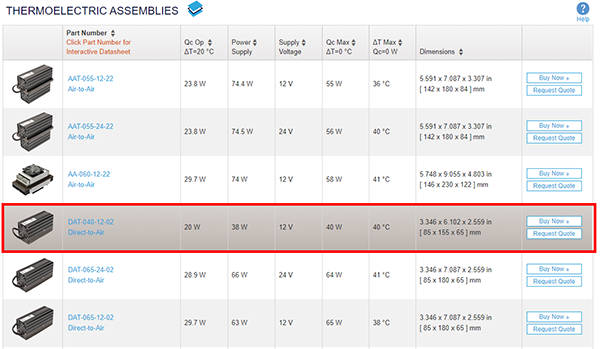
Figure 4: Thermoelectric Cooler Assemblies Thermal Solutions
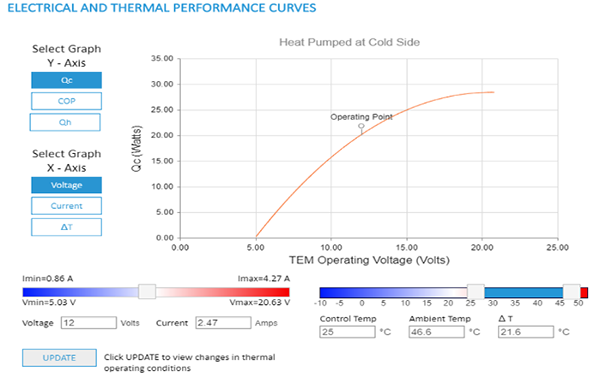
Figure 5: DAT-040-12-02 Qc vs Voltage
The Thermoelectric (TEC) voltage can also be reversed on a thermoelectric cold plate to heat the laser (hot plate) with as much as 84 Watts of heat (Qh). The only thermal resistance necessary to take into account with the thermoelectric cold plate is the interface thermal resistance of 0.08 °C/W for thermal grease, adding 1.6 °C to the ΔT specification.
Developing trial designs to solve what-if scenarios
Design engineers can use the Thermal Wizard’s four (4) Qc calculators to model new product designs in order to observe how the trial design performs under various What-If scenarios. Linking actual thermal products and their real-world performance to application models accelerates trial design results, shortening design times.
For example, a piece of medical laboratory analytic or diagnostic equipment requires samples to be stored at 0°C. Using the Thermal Wizard’s Enclosure Cooling Calculator and selecting the Sample Cooler example, we can change the dimensions to (250mm x 250mm x 200mm) with 30mm of foam insulation. The passive cooling load (Qc) is 9 Watts at a ΔT of 25°C (see Figure 6).
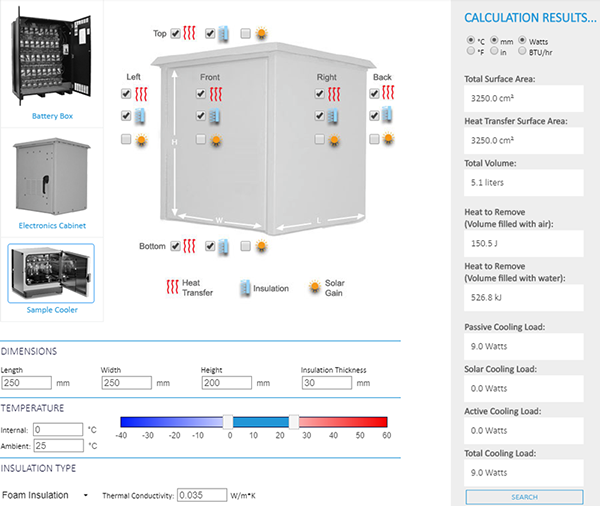
Figure 6: Enclosure Cooling - Sample Cooler Example
We can simulate the requirement to have a glass door instead of an insulated door on the front of the sample cooler by removing the insulation on the front of the enclosure. This yields a Qc of 34.7 watts, a 286% increase in the passive cooling load. What if we reduce the insulation thickness to 15mm? Not surprisingly, this nearly doubles the passive cooling load to 17.1 Watts. The Thermal Wizard not only includes a model for enclosure (cabinet) cooling, but also a device cooling (cold plate) model, air cooling model, and a liquid cooling calculator. All of these model calculators link the Qc and ΔT specifications to the Thermoelectric Coolers, Thermoelectric Cooler Assemblies and Liquid Cooling Systems product selector for quick access to the actual products required to meet your application’s need.
Choosing the optimum level of complexity to engage a Thermal Solutions Vendor
Depending on manufacturing capabilities and risk tolerance, engineers often need thermal management assistance, recommendations or guidance on the optimum level of integration to engage with a thermal solutions vendor. The Thermal Wizard provides thermal solutions at the component, sub-assembly, and complete turn-key level. To illustrate this process we can use the device cooling calculator to calculate the cooling requirements for a 96 well 1.5 mL microcentrifuge tube sample block. Assuming a sample block size of 203mm x 203mm x 38mm made out of aluminum, the passive cooling load is 4W at a ΔT of 21°C with 15mm of foam insulation (see Figure 7).
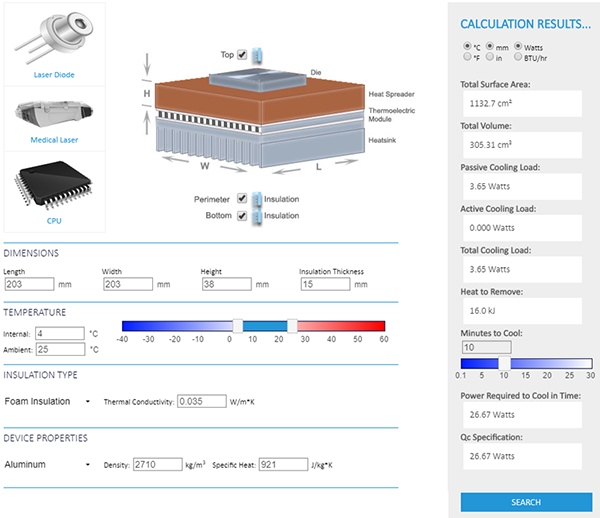
Figure 7: Device Cooling – Cold Plate Example
However, we would like to cool it down in a reasonable amount of time. Using 10 minutes for cooling time yields a Qc requirement of 27 Watts. Clicking the search button yields three thermoelectric cooler solutions and a number of thermoelectric cooler assembly solutions. If you engage Laird Thermal Systems at the component (thermoelectric cooler) level, you will be responsible for the heatsinking, power supply and mounting of the thermoelectric cooler within your assembly. Laird Thermal Systems can provide application support to help you accomplish this. However, if you engage at the sub-assembly (thermoelectric cold plate) level, you can select the DA-075-12-02 and view thermal performance, drawings for mechanical attachment to your sample block and power supply requirements. Another level of engagement is also available through the Custom Cooling Solutions – Contact a Laird Thermal Expert for more information. You can discuss modification options to standard parts for better integration into your overall assembly.
Prototyping Custom configurations when Standard products fall short
Design engineers with thermal management issues need to know who to contact when standard thermal management product offerings are insufficient. As with the previous example, you can use the Thermal Wizard to prototype new designs that meet your thermal cooling requirements, but may fall short with the addition of mechanical or temperature requirements. Laird Thermal Systems has an experienced application engineering staff ready to help customize a solution. The Thermal Wizard can help you identify the right questions to ask in much less time.
Where to find Thermal Management Products quickly to meet tight schedules
The Thermal Wizard displays the quickest means of obtaining samples for prototyping. Whenever the Thermal Wizard displays a product, either in a selection list or in an active datasheet, a Buy Now >> button is always there to indicate a source with inventory. Clicking the Buy Now >> button links directly to Octopart and shows authorized distributors with availability and pricing. The Thermal Wizard Request a Quote form is also available if you require a firm quote from Laird Thermal Systems.
Laird Thermal Systems’ Commitment to Customer Service
Laird Thermal Systems developed the Thermal Wizard to assist customers dealing with challenging thermal design problems in a competitive environment, where time-to-market is critical. Simplifying the selection of cooling solutions, especially thermoelectrically cooled solutions, is a powerful tool in any engineer’s toolbox. Linking that cooling solution selection ability to application model calculators further benefits the customer with quick answers to complex questions. Providing direct links to stocking distributors helps source prototype parts quickly, reducing time to market. Backing the Thermal Wizard with qualified application thermal experts completes Laird Thermal Systems’ outstanding commitment to customer service.
Contact Laird Thermal Systems
Have a question or need more information about Laird Thermal Systems? Please contact us.