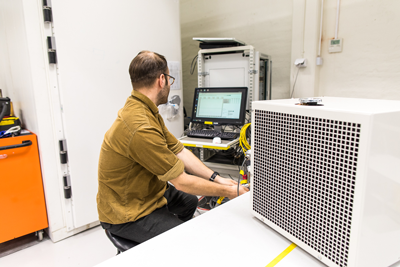

Laird Thermal Systems has conducted several decades of validation testing on various combinations of thermal components to optimize cooling power and efficiency at various heat loads while minimizing noise. Our reliability and functional testing can be tailored according to customer specifications and applicable industry standards.
- Reliability testing – ensures mechanical integrity of the liquid cooling system
- Functional testing – ensures that the system meets expected performance
- Compliance - verifies that the liquid cooling unit meets applicable industry standards
- Quality Control – end of line test to ensure high-quality products
Learn more about testing for liquid cooling systems below or contact Laird Thermal Systems for consultation.
Mechanical Testing
OEMs within specific application of the medical sector are required to perform g-force testing on all components to ensure operational safety of the equipment. With inhouse gantry testing equipment, Laird Thermal Systems can deliver liquid cooling systems tested to withstand high g-forces. This allows us to test and evaluate components as well as systems from the designing to manufacturing process, saving time and cost for OEM customers. We also test mechanical strength of the product to make sure that mountings or fasteners do not fail due to high g-forces.
Laird Thermal Systems Gantry Testing Capability
- Capable of testing up to 100 g-forces
- Ability to test single components to complete systems mounted in various orientations
Performance Testing
Our test engineers will run multiple cooling capacity tests to make sure the liquid cooling system delivers expected performance at various heat loads. The result will be presented in a performance graph showing cooling capacity (Watts) versus temperature differential Delta T (∆) at a given ambient temperature. All our data sheet performance graphs have a tolerance of 10%.
How is the test performed?
- The liquid cooling system is placed in a climatic chamber at various environmental temperatures.
- A liquid circuit with inline heaters is used to generate heat load.
- For Liquid Heat Exchangers, temperature differential (ΔT) for performance graph is calculated by subtracting ambient temperature and temperature of liquid out to customer application.
- For Liquid Chillers, performance is graphed as heat load at a given setpoint at various ambient conditions.
This test is typically only conducted for chiller units, because temperature control is a critical aspect of the system’s performance.
How is the test performed?
- The chiller will run at normal operating conditions in a climatic chamber at the temperature intended for use.
- We will measure temperature stability to ensure it meets application requirements. Our Nextreme Chiller Platform achieves a temperature stability of +/-0.1°C which is sufficient for most applications.
- During design validation, testing is also conducted to optimize the systems response to both positive and negative changes in heat load and setpoint.
Understanding air flow and temperature distribution is the key to developing the optimum thermal management system. Laird Thermal Systems engineers utilize wind tunnels to program the desired air flow in order to optimize cooling performance while minimizing noise and size of heat exchangers.
Laird Thermal Systems wind tunnel capabilities
- Volume air flow measurement
- Air speed measurement
- Capable of creating variable laminar homogenous air flow
- Controllable heat injection
- Variable pump speed
- Liquid/Air pressure drop measurements
- Liquid/Air flow measurements
- Liquid/Air temperature measurements
No matter the industry, manufacturers of any equipment are always seeking ways to reduce noise. In thermal systems, noise is a result of vibrations generated by components such as pumps, fans and air ducts. Because it is more complicated to reduce noise when a product is already built, Laird Thermal Systems measures and evaluates noise throughout the entire process, from the design stage and selecting components to product sign-off.
How is the test performed?
- Laird Thermal Systems utilizes acoustic analyzers with Class 1 microphone in accordance with IEC 61672 standard, enabling reliable long-term and frequency measurements.
- We perform noise measurements in accordance with ISO 12001:1996, accuracy grade 3 (survey grade) to achieve comparable results.
- If customers require standards beyond our inhouse capabilities, for example EN 3746 or EN61010-1, testing can be performed in accredited labs with our external partner.
Compliance
Laird Thermal Systems is committed to providing products that meet regulatory requirements and are environmentally safe.
Our liquid cooling systems comply with
Our liquid cooling systems comply with
- RoHS - the Restriction of Hazardous Substances
- REACH - the Registration, Evaluation, Authorisation and Restriction of Chemicals (Europe)
- TSCA - Toxic Substances Control Act (US)
- CA PROP 65 - Safe Drinking Water and Toxic Enforcement Act (US, California)
Electromagnetic Compatibility (EMC) and Electromagnetic Interference (EMI) testing are critical steps to ensure product safety and performance.
While EMI can be defined as the phenomenon of electromagnetic disturbance, EMC is an equipment characteristic. EMC testing will determine the product’s ability to properly function independent of environments with electromagnetic interference as well as ensuring that surrounding equipment will not be affected.
While EMI can be defined as the phenomenon of electromagnetic disturbance, EMC is an equipment characteristic. EMC testing will determine the product’s ability to properly function independent of environments with electromagnetic interference as well as ensuring that surrounding equipment will not be affected.
How is the test performed?
- Laird Thermal Systems engineers perform this testing in accredited labs at our external partner.
- During testing the unit will operate at intended operating conditions in similar environmental condition as specified in applicable standards or according to customer specifications.
- Laird Thermal Systems EMC testing complies with:
- Residential, commercial and light -industrial environments immunity standard EN 61000-6-1:2007
- Residential, commercial and light -industrial environments emission standard EN 61000-6-3:2007 and EN 61000-6-3/A1:2011
- Industrial environment immunity standard EN 61000-6-2:2005
- Industrial environment emissions standard EN 61000-6-4:2007 and EN 61000-6-4/A1:2011
Underwriter Laboratories (UL) is a leading global certification company known for conducting some of the most rigorous and extensive safety testing programs on the market. Not only do these tests identify and eliminate immediate danger such as electrical shock, hot surfaces, sharp edges, and moving parts, but they also ensure items such as complying with maximum current draw in intended installation regions. Due to the complexity of liquid cooling systems, most of the UL testing program is often required according to certain standards.
How is the test performed?
- Laird Thermal Systems will provide UL with a testing unit and all relevant documentation (component datasheets, system diagrams, risk analysis, etc.) in good time before product release.
- UL will test the unit at both normal and above normal operating conditions to make sure it conforms with regional standards.
- Test results will be fully transparent and UL will provide recommendations on how to improve mechanical and electrical design to meet product requirements.
- UL certification will be successful once the product passes all testing criterion. Final test reports are available upon request.
End-of-Line Testing
The liquid cooling system will go through a visual inspection where following criteria will be checked:
- Dimensions are accurate
- No scratches or defective paint
- Corners are chamfered, without sharp edges
- Connection points are tightened
- No missing or loose screws
- System is free of liquid from testing
- Inlet and outlet fittings are protected for shipment
- Product is appropriately labeled
Products will go through a Hi-Pot or dielectric withstand test to ensure that insulation of the liquid cooling system is sufficient to prevent current leakage at normal operating voltage conditions. This is a required product test by UL.
This is a critical safety test to verify that the unit does not leak excessive current when contacted by the user, potentially resulting in severe injury. This is a required product test by UL.
Coolant leakage has a significant impact on product performance and is one of the biggest challenges when designing a liquid cooling system. We are proud to offer the capability to perform helium vacuum testing on liquid-based cooling units during production and validation testing to ensure tight and reliable systems.
How is the test performed?
- The Liquid Cooling system is vacuumed in the chamber before testing to ensure maximum accuracy.
- The system is filled up with nitrogen to verify that there are not major leaks.
- If no leaks are detected, the system will be vacuumed again and pressurized with helium. Because helium gas has the smallest molecule size it offers the best chances to detect the tiniest pinhole leaks.
- A helium detector will identify and measure the concentration of helium in the testing chamber to make sure leakage from the unit has not exceeded an acceptable level.
- A leak detector helps us locate the leakages in order for us to rework the unit and ensure the system is properly sealed.
Liquid cooling systems will undergo extensive performance testing to verify that they meet expected requirements. Together with the customer (internal or external), Laird Thermal Systems engineering and operations team will determine the best methods to verify performance of each system. These can be for example coolant flow, temperature stability and cooling capacity.