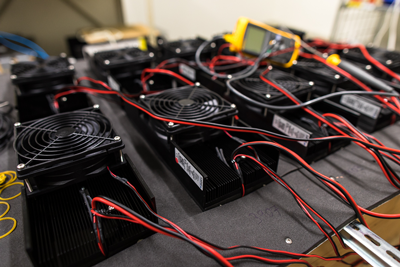
Laird Thermal Systems has conducted several decades of validation testing on various combinations of thermal components to optimize cooling power and efficiency while reducing operational noise. Our reliability and functional testing can be tailored according to customer specifications and applicable industry standards.
- Reliability testing – will determine the thermoelectric cooler assemblies' mechanical integrity and ability to survive in the intended application or extreme environmental conditions
- Functional testing – ensures that the thermoelectric cooler assembly meets expected performance
- Compliance – verifies that the thermoelectric cooling unit meets applicable industry standards
- Quality Control – end of line test to ensure high-quality products
Passing Criteria
The most common method to evaluate thermoelectric cooler assemblies is to measure AC-resistance (ACR) before and after the test is performed. Ideally, AC resistance will not change after testing. If the ACR change is greater than 5% it would not pass the test.
Learn more about thermoelectric cooler assembly testing below or contact Laird Thermal Systems for consultation.
Mechanical Testing
How is the test performed?
The packaged unit will be dropped on surfaces, edges and corners from the height specified in the packaging requirements.
Environmental Testing
How is the test performed?
A salt spray test machine will apply salt water solution to the thermoelectric cooler assembly in a closed chamber.
AC- Resistance will be measured before and after the test to determine any deviations. We will also check potential color fading, discoloration, cracking, blistering twisting, etc. to make sure there are no corrosion.
How is the test performed?
- On/Off Power Cycling Power is turned on and off alternately at a specified number of cycles in a set ambient condition. Laird Thermal systems has the capability to test up to 50K+ cycles.
- Reverse Power Cycling – the thermoelectric cooler assembly is subjected to thermal stress generated by sudden changes between positive and negative power conditions. This is commonly used for PCR applications when heating and cooling occurs alternately. Laird Thermal Systems can test up to 200K+ cycles within a temperature range between 0~120℃. We also offer control of ramp up rates.
Performance Testing
How is the test performed?
Air-to-Air units- The thermoelectric cooler assembly will be mounted in a test box with expected leakage rate and placed in a climatic chamber at desired ambient temperature.
- Heaters in the test box simulate heat load on the unit.
- Temperatures will be measured both at inlet and outlet of the internal and external side of the thermoelectric assembly.
- Instead of using a test box with internal heater, plates with heaters are mounted directly onto the D-plate. D-plate and heaters are insulated against ambient.
- Temperature differential (ΔT) for performance graph is calculated on inlet of external side and temperature of heater plates.
- Instead of using a test box, a liquid circuit with inline heaters is used to generate heat load.
- Temperature differential (ΔT) for performance graph is calculated at inlet temperature of external side and average temperature of liquid inlet and outlet.
How is the test performed?
- Our temperature control tests are carried out in climatic chambers to simulate the intended application environment.
- The highest possible control temperature accuracy and/or stability will be determined by the temperature controller during operation.
Methods used are
- Air speed measurement
- Controllable heat injection
- Variable pump speed
- Liquid/Air pressure drop measurements
- Liquid/Air flow measurements
- Noise measurement
How is the test performed?
- Laird Thermal Systems utilizes acoustic analyzers with Class 1 microphone in accordance with IEC 61672 standard, enabling reliable long-term and frequency measurements.
- We perform noise measurements in accordance with ISO 12001:1996, accuracy grade 3 (survey grade) to achieve comparable results.
- If customers require standards beyond our inhouse capabilities, for example EN 3746 or EN61010-1, testing can be performed in accredited labs with our external partner.
Compliance
Our thermoelectric cooler assemblies comply with
- RoHS - the Restriction of Hazardous Substances
- REACH - the Registration, Evaluation, Authorisation and Restriction of Chemicals (Europe)
- TSCA - Toxic Substances Control Act (US)
- CA PROP 65 - Safe Drinking Water and Toxic Enforcement Act (US, California)
While EMI is known as the phenomenon of electromagnetic disturbance, EMC is an equipment characteristic. Not only will EMC testing determine the product’s ability to properly function in environments with electromagnetic interference, but also ensuring that it will not affect other equipment in the same environment. Both these aspects are important in the development process to ensure product safety and performance.
How is the test performed?
- Laird Thermal Systems engineers conduct EMC testing in accredited labs at our external partner.
- The test unit will run at intended operating conditions and the environment is set up according to applicable standard or customer specified standard.
- Our EMC testing complies with:
- Residential, commercial and light -industrial environments immunity standard EN 61000-6-1:2007
- Residential, commercial and light -industrial environments emission standard EN 61000-6-3:2007 and EN 61000-6-3/A1:2011
- Industrial environment immunity standard EN 61000-6-2:2005
- Industrial environment emissions standard EN 61000-6-4:2007 and EN 61000-6-4/A1:2011
How is the test performed?
- Laird Thermal Systems will provide UL with a testing unit and all relevant documentation in good time before product release.
- UL will test the unit at both normal and above normal operating conditions to make sure it conforms with regional standards.
- Test results will be fully transparent, and UL will provide recommendations on how to improve mechanical and electrical design to meet product requirements.
- UL certification will be successful once the product passes all testing criterion. Final test reports are available upon request.
End-of-Line Testing
- Dimensions are accurate to print
- No scratches or peeling paint on product surface
- Corners are chamfered, without sharp edges
- Connection points are tightened
- No missing or loose screws
- Inlet and outlet of pipes are blocked
- Product is appropriately labeled