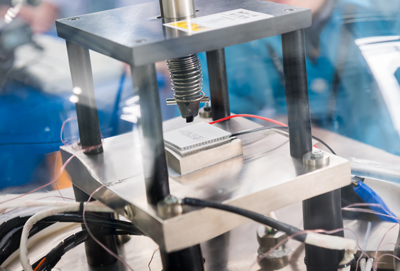
Laird Thermal Systems provide extensive testing programs for thermoelectric coolers to ensure high product reliability and performance:
- Reliability testing – determines the thermoelectric cooler’s mechanical integrity and ability to survive in an extreme environmental condition
- Functional testing – verifies that the thermoelectric cooler meets expected performance
- Compliance –ensures that the product meets applicable industry standards
- Quality Control – end of line testing for final quality check
Testing Pass Criteria
Standard mechanical or environmental testing is conducted to Telcordia GR-468 Core or MIL-STD. Standard testing does not accommodate all application criteria and often custom environmental testing is conducted based on OEM specifications. The most common method to assess health of a thermoelectric cooler is by measuring AC-resistance (ACR) before and after the qualification test has been conducted. A significant drop of AC resistance indicates that the thermoelectric cooler has degraded. If the ACR change is greater than 5% it would not pass the test.
Learn more about testing for thermoelectric coolers below or contact Laird Thermal Systems for assistance.
Mechanical Testing
How is the test performed?
- The thermoelectric cooler is mounted on the test fixture which is then mounted on the test equipment platform in one of three axes.
- The thermoelectric cooler is subjected to vibrations during multiple sequences.
How is the test performed?
The packaged unit will be dropped on surfaces, edges and corners from the height specified in Telcordia requirements.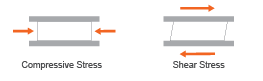
How is the test performed?
- The thermoelectric cooler will be attached to the module holding fixture.
- With one plate of the thermoelectric cooler held in place, a shear force will be applied to the other plate according to the customer specification.
HASS- Highly Accelerated Stress Test will detect flawed thermoelectric coolers caused by poor manufacturing processes. The testing procedure is similar to HALT but stress levels are less extreme.
How is the test performed?
- The thermoelectric cooler is powered on and placed in a hot oven.
- The thermoelectric cooler is subjected to mechanical stress by increasing temperature changes. For HALT testing, the extreme conditions will lead to failure of the thermoelectric cooler.
- The test analysis will determine if the module construction must be enhanced (HALT) or if potential defects have been caused by poor manufacturing processes (HASS).
Environmental Testing
How is the test performed?
The thermoelectric cooler will be placed in a storage chamber at a temperature and time specified by a certain standard or customer application requirement. Laird Thermal Systems can perform- Low temperature storage testing
- High temperature storage testing
How is the test performed?
The thermoelectric cooler will be placed in a storage chamber at a defined temperature and humidity.
How is the test performed?
- On/Off Power Cycling – Thermoelectric cooler is placed in a fixture and powered on and off to a set duration for a specified number of cycles. Laird Thermal Systems has the capability to test more than 5000 cycles.
- Reverse Power Cycling – the thermoelectric cooler is exposed to thermal stress generated by sudden changes between positive and negative power conditions. This is often used for PCR applications when heating and cooling occurs alternately. Laird Thermal Systems can test up to 200K+ cycles, within a temperature range between 0~120℃.
How is the test performed?
The thermoelectric cooler will be exposed to extremes of high and low temperatures in non-operational mode. As the module contracts and expands from repeated cooling and heating cycles over a long period of time, the thermoelectric cooler will be subjected to mechanical stress.
Performance Testing
How is the test performed?
- The thermoelectric cooler is placed on a heatsink with the cold side facing upwards in a vacuum environment. A copper block is put on the cold side as thermal load.
- Current will be applied to the thermoelectric cooler to reach the calculated Imax that produces the maximum possible temperature differential (∆Tmax).
- Current of thermal load will then change so the temperature of the hot and cold side is equal, resulting in ∆T= 0
- The maximum cooling capacity (Qmax) is determined by the required power input to thermal load
Compliance
Our thermoelectric coolers comply with
- RoHS - the Restriction of Hazardous Substances
- REACH - the Registration, Evaluation, Authorisation and Restriction of Chemicals (Europe).
- TSCA - Toxic Substances Control Act (US)
- CA PROP 65 - Safe Drinking Water and Toxic Enforcement Act (US, California)
Due to lack of industry standards in other markets, OEM’s have adopted Telcordia standards in reliability testing for products used in other critical applications, such as machine vision, autonomous and optoelectronic applications.
Laird Thermal Systems uses state-of-the-art proprietary testing equipment and methodologies to test Telcordia Requirements. Our testing chambers can simulate almost any environment to evaluate potential impact of transportation, operation and storage.
Contact us and our Engineering team will provide a testing program following Telcordia standards.
End-of-Line Testing
- Ensure temperature uniformity throughout the device
- Identify hot-spots, such as poor soldering in a thermoelectric module
- Dimensions are accurate to print
- No cosmetic defects, such as solder balls, cracks in TE elements, cracks in ceramic substrates, corrosion, cleanliness solder adhesion