Introduction
Electron microscopes are a powerful laboratory tool used to observe samples across many scientific disciplines. These advanced analytical instruments enable researchers to qualitatively and quantitatively analyze samples in fields like metallography, metrology, anthropology, zoology, epidemiology and more. Temperature control plays a dynamic role in ensuring the proper operation of electron microscopes. This includes sample temperature stabilization (read Heating and Cooling of Incubator Chambers application note), as well as thermal control of sensitive equipment electronics. Thermal fluctuatio¬ns can degrade the quality of the microscopic imaging, and lead to a break down in the composition of the sample under examination.
Compressor-based chillers with integrated temperature control offers an advanced thermal management solution that keep sensitive electronics and samples at the optimum temperature for operation and examination respectively. However, because of new industry restrictions on hazardous refrigerants central in traditional chiller technology, electron microscope manufacturers now require a more environmentally friendly, efficient and maintenance-free chiller solution. The eco-friendly Nextreme™ Chiller quietly cools temperature sensitive components below ambient temperature to ensure optimum image quality.
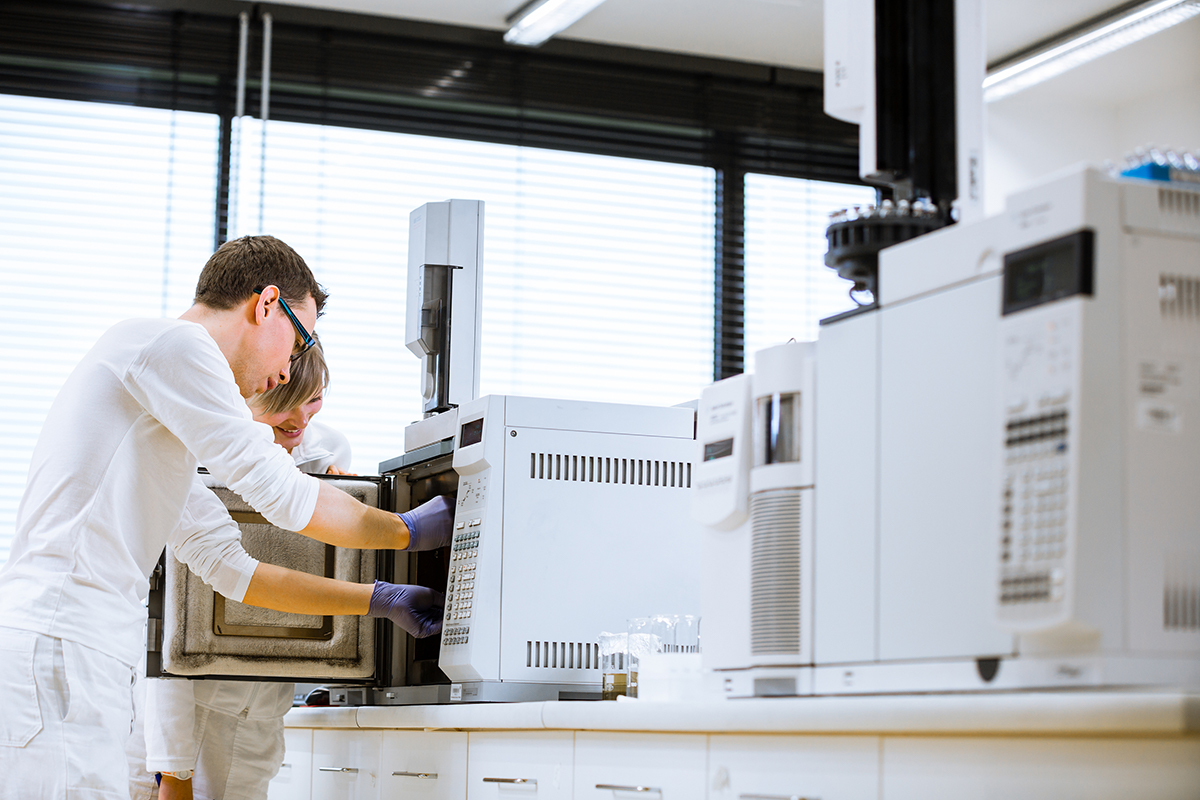
Lab instrumentation tools such as electron microscopes
require an advanced thermal management solution for
precise temperature control of electronics and samples.
Background
An electron microscope uses a beam of accelerated electrons as a source of illumination to investigate the ultrastructure of a wide range of biological and inorganic specimens including microorganisms, cells, large molecules, biopsy samples, metals, and crystals.
Electron microscopes have a higher resolving power than light microscopes and can reveal the structure of smaller objects. While standard light microscopes are limited by diffraction to about 200 nm resolution and useful for magnifications below 2000X, a scanning transmission electron microscope has achieved better than 50 pm resolution in annular dark-field imaging mode and magnifications of up to about 10,000,000X. Modern electron microscopes produce electron micrographs using specialized digital cameras and frame grabbers to capture the images.
There are several types of electron microscopes with different configurations and techniques to analyze specimens. However, all electron microscopes use a high voltage electron beam to illuminate a specimen and create an image. The electron beam is produced by an electron gun. Depending on the type of electron microscope, the beam is sent through a combination of lenses, apertures, the specimen sample being analyzed, and a viewing screen where the camera is mounted to take the image.
Electrons behave like light only when they are manipulated in a vacuum. The whole column from gun to screen including the camera is evacuated. The highest vacuum is around the specimen and in the gun; a lower vacuum is found in the projection chamber and camera chamber. To improve image quality, OEMs implement thermal management systems that cool the digital cameras used for image creation. Active cooling is required to deliver optimal image resolution independent of the operating environment. In addition, advanced electron microscopes also have temperature control functionality for the specimen holder.
The electron beam can be controlled or manipulated via a magnetic field according to the left hand rule. Electromagnets create a magnetic field that allows for the formation of a magnetic lens of variable focusing power. The coils, which produce the magnetic field, are located within the lens yoke. The coils can contain a variable current but typically use high voltages and therefore require significant insulation in order to prevent short-circuiting the lens components. These coil windings require a thermal management solution to remove the heat generated when creating the magnetic field.
Application Challenges
Designers face a number of challenges when developing electron microscopes. As mentioned, several key microscope components, including the image recording electronics, the electromagnetic coils, and the sample port require stable thermal control below ambient temperatures. To go below ambient temperatures, refrigeration systems are required. This isn’t possible with other cooling technologies like liquid heat exchangers, which uses air to cool a cooling loop.
In addition to meeting thermal control requirements for these three electron microscope elements, cooling solutions must also meet smaller size, lighter weight and reduced power consumption requirements. To optimize lab space, OEMs continue to look for ways to decrease device size while increasing device functionality. As a result, more electronics are packaged into smaller housings, increasing the heat flux density and thermal challenges. This waste heat must be managed and dissipated efficiently in order to enhance the imaging capability of the electron microscope, while reducing power consumption and providing quieter operation (both lower noise and vibration). Electron microscope designs must also take airflow into account. Paths for incoming and exhaust air must be considered to maximize the cooling performance.
Electron microscopes are sensitive to disturbances in the surrounding environment like vibration. Some liquid pump models cause more vibration as a result of higher pulsations in the fluid lines. This is the case with a rotary vane pump or centrifugal pump. Turbine pumps have significantly less pulsation, which results in better imaging by the microscope.
The thermal management system also provides condensation protection for the electronic microscopes. Moisture forms on cold surfaces as temperature drops below the dew point. If this moisture seeps into the electronics, or onto the lenses, it can cause deterioration and ultimately failure of the electronics and affect image quality. Using properly designed insulation materials can provide a cooling solution resistant to moisture intrusion.
Electron microscopes must follow UL61010-1 or IC 61010-1 lab safety standards. These standards include specifications for electromagnetic compatibility and electromagnetic emissions to ensure electron microscopes can operate in the same room as other electronic equipment without interference. When designing an electron microscope OEMs will either ask for a certification from the chiller manufacturer, or certify it themselves as part of the installed system.
In addition, many governments continue to develop strict environmental legislation aimed at curbing climate change, which restricts usage of refrigerants in several refrigeration and freezer systems. The phase down on environmentally harmful refrigerants, like HFC refrigerants including R134a and R404A, has led to the development of new, eco-friendly refrigeration systems. These systems use natural refrigerants that have a reduced eco-footprint. However, the flammable nature of some natural refrigerants can make them hazardous to transport, and each one presents design challenges such as increased pressure, high toxicity, flammability, asphyxiation, and relatively poor performance. Another restriction in Europe is ROHS (Reduction of Hazardous Substance), which means that you cannot use led, mercury, cadmium and other heavy metals in electronic products.
Comparing Cooling Technologies
Modern compressor-based liquid cooling systems meet the electron microscope design requirements mentioned above. Compressor-based liquid cooling systems, which are self-contained units that recirculate coolant to a predefined temperature set-point, allow for optimal thermal stabilization and more precise temperature control. Standard and custom liquid cooling systems are able to dissipate the large amount of heat generated in densely packed electronic environments like electron microscopes.
Compressor based refrigeration systems offer a high coefficient of performance (COP). If they are cooling a heat load of 3 kW, they only require 1 kW of energy to do the work to cool it, which is more efficient compared to other technologies like thermoelectric cooling. Compressor-based systems tend to be smaller than alternative technologies like liquid-air-heat exchangers when achieving set-points near ambient temperatures because they make use of the refrigerant’s latent energy to increase heat exchanger efficiency. Thermoelectric devices on the other hand are smaller, but as mentioned, they are less efficient.
If the product is operating in ambient temperature, liquid-heat-exchangers are more efficient. However, liquid-to-air heat exchangers do not cool below ambient like compressor-based and thermoelectric systems.
Central facility cooling systems is another option previously used to cool electron microscopes. Since these systems are used to cool equipment in the entire building it can be difficult to satisfy all of the instrumentation’s cooling requirements with one centrally controlled system. In addition, it cannot guarantee a constant temperature and flow rate.
Laird Thermal Systems Solution
The Nextreme™ Chiller Platform from Laird Thermal Systems offers reliable and precise temperature control for electron microscopes. Utilizing high-performance variable speed motors, it offers lower noise operation and reduced energy consumption by up to 50% compared to conventional compressor-based systems.
The Nextreme™ Chiller offers precise temperature control, achieving an accuracy of ±0.1°C as the unit heats and cools fluid to maintain the thermal set point. Electron microscope imaging systems, electromagnetic coils and test samples benefit greatly from the precise temperature control, ensuring the development of high quality images.
By using environmentally-friendly R513A refrigerant, the Nextreme™ Chiller achieves similar performance with half the Global Warming Potential (GWP) compared to traditional hydrofluorocarbon (HFC) refrigerants. The chillers not only meet CE and RoHS requirements, but UL61010-1 and IC 61010-1 lab safety standards as well.
Featuring a LCD touchscreen display, the Nextreme™ Chiller Platform is designed with the laboratory technician in mind. It allows the technician to control temperature setpoints, coolant type, flow and alarm settings while coolant level is easily monitored through the indicator window located on the front panel. For maximum uptime, the Nextreme™ Chiller can be equipped with the optional “hot swappable” 5-micron water filter for filtering particulates from the coolant circuit, which means that the system can operate also during maintenance.
The Nextreme™ Chiller features an optical fluid level sensor with no moving parts, which increases reliability and uptime when compared to chillers equipped with mechanical fluid switches. If the fluid level drops below normal operating conditions, the user will be alerted by the programmable alarm. The chiller will also alert users when low- or high-pressure limits have been exceeded in order to protect the equipment. In addition, the Nextreme™ Chiller utilizes a low pulse turbine pump to ensure low vibration operation for superior image quality.
The Nextreme™ Chiller Series is available in three standard cooling capacities including 1600W, 2800W and 4900W models. All Nextreme™ Chiller models are configurable in order to meet specific application requirements.
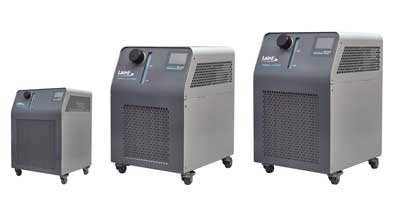
The Nextreme™ Recirculating Chiller Platform is available in three different capacities, 1600W, 2800W and 4900W.
The Nextreme™ Chiller can operate on 208-240VAC, 60Hz and 200-230VAC, 50Hz. While many other manufactures have a different model for Europe and North America, the single Nextreme™ Chiller can be purchased and operated globally. This is important for when a company chooses to test equipment in one country before shipping to a different region. It also means that companies can carry less inventory as a single chiller can ship anywhere.
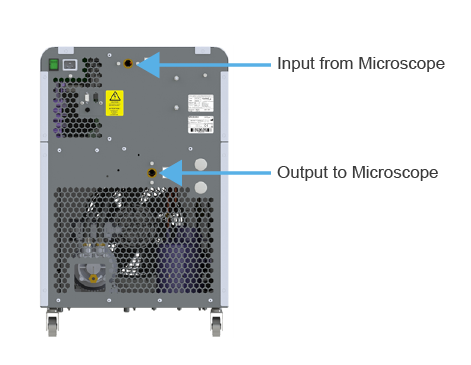
The Nextreme™ Chiller input and output connections
Conclusion
Properly cooling an analytic instrument like an electron microscope requires a sophisticated thermal management system. Modern compressor-based refrigeration systems are more advanced and efficient than previous versions. Compact chiller systems offer a higher coefficient of performance with maximum uptime and minimal power consumption compared to the application’s heat load. The versatile Nextreme™ Chiller provides quiet operation in a smaller and lighter package compared to previous models. The Nextreme™ recirculating chiller platform enables more focused and improved performance resulting in a precise image with better resolution.
More information on the Nextreme™ Chiller Platform can be found by visiting lairdthermal.com/nextreme-chiller
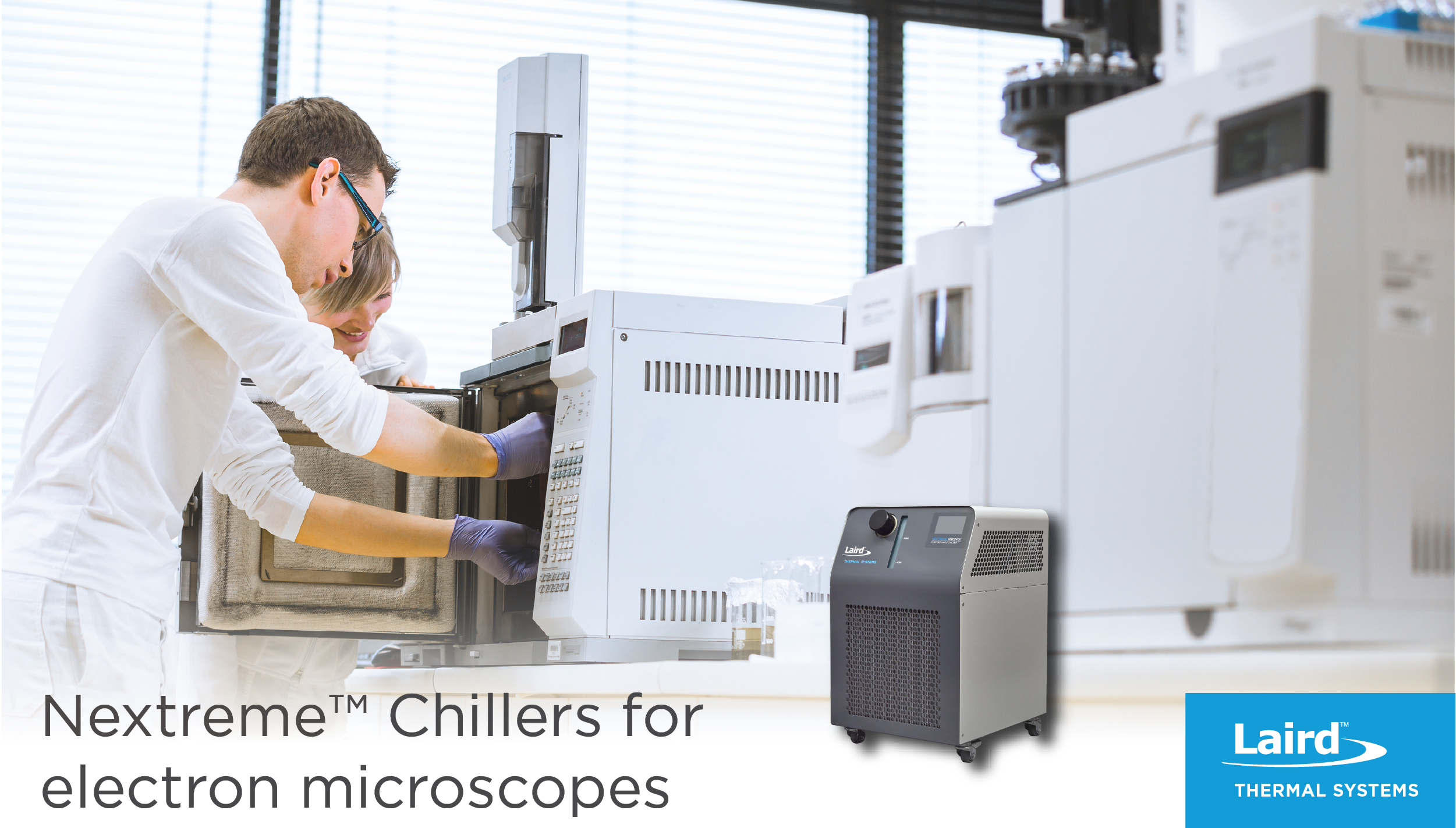