Introduction
Industrial lasers are used for a wide range of applications including cutting, welding, micro-machining, additive manufacturing and drilling. No matter the application, industrial laser systems generate a significant amount of heat. There are several different types of industrial laser technologies, ultimately distinguished by the power density of the laser and its use. The commonality of every laser system is the need for advanced cooling of the power source and the laser optics. Temperature stability of these components is critical to ensuring the performance of the laser system. Chillers have been used to cool industrial laser systems for decades. However, new industry refrigerant restrictions and performance requirements have led industrial laser manufactures to demand a more eco-friendly, efficient and maintenance-free chiller solution. The efficient and environmentally-friendly Nextreme™ Recirculating Chiller platform quietly cools temperature sensitive components below ambient temperature to ensure optimum laser performance.
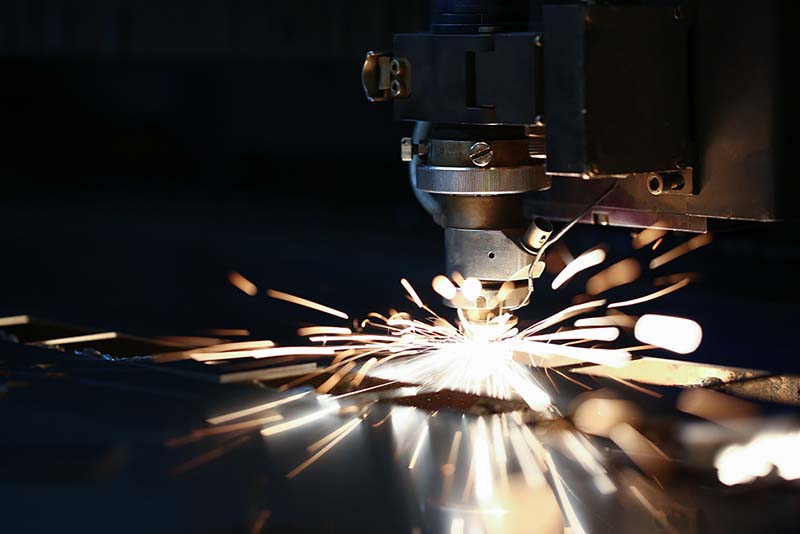
Industrial lasers used for cutting hard materials require a cooling solution
to ensure stability of the laser beam.
Application Overview
Efficiently cooling lasers can be a significant challenge. For example, fiber lasers have better cooling characteristics over other media due to their specific arrangement, which enables them to spread the heat over a larger surface area. Ion lasers are characterized by the generation of extreme heat during lasing and the need for elaborate cooling measures. Carbon dioxide (CO2) lasers emit heat energy in the far-infrared and microwave region of the spectrum. To ensure proper, long-term performance of the laser, heat needs to be quickly and effectively dissipated by the cooling system.
Depending on system size and configuration, waste heat may be transferred by a coolant or directly to air. For laser systems that generate heat in excess of a few hundred watts, a liquid coolant solution is warranted. Coolant is circulated through a chiller or heat transfer system to pump heat away from sensitive laser components, and maintain a constant operating temperature.
Some coolant solutions feature cooling system pumps with greater pulsation. Pulsating pumps still offer the required system cooling, but create vibration within the cooling system. In laser systems, this has similar effects to thermal instability and results in a less focused laser beam and lower quality performance, which is critical in cutting and engraving applications. Industrial lasers are commonly used for cutting hard materials like steel. Basically, the laser beam melts through whatever material it is focused on. When cooled efficiently, the laser beam creates a finer, more precise cut or engraving. If the laser beam operates outside the optimum temperature range, it is not as focused and creates a rougher, less precise cut or engraving.
Application Challenges
Many challenges exist in terms of the design, implementation and maintenance of liquid cooling systems for industrial laser systems. If an industrial laser system goes down, it can shut down the entire manufacturing process. This can significantly impact production and incur large manufacturing costs. Therefore, robustness and maintenance-free operation of the chiller cooling system is critical to ensure maximum system uptime.
As previously mentioned, temperature stability is vital for both the industrial laser power supply and laser optics. Depending on the type of laser system and application, heat generated from the laser can be far more than kilowatts. For optimal performance, the laser optics typically require a stable operating temperature of 20°C ± 0.1°C, while ambient temperature may fluctuate between 23°C to 35°C in a room temperature environment.
Miniaturization of industrial laser systems has led OEMs to pack more electronics into a smaller footprint. This increases the heat flux density and adds thermal load to the unit, making the industrial laser cooling solution even more important to the efficiency and performance of the laser power source and optics. To meet the required cooling capacity in a more compact form factor, the thermal management solution must have a high coefficient of performance (COP) for cooling well below ambient temperatures. Waste heat must be managed and dissipated efficiently in order to increase laser performance, while reducing power consumption and providing quieter operation (both lower noise and vibration).
Loud, vibrating machines can create an unpleasant and dangerous environment. Equipment cooling units can play a significant role in the decibel level on a manufacturing floor. New industrial laser systems require quiet operating thermal management solutions. Noise is also a consideration for laser system in need of a retrofitted chilling unit.
Many governments are requiring OEMs to phase out use of traditional ozone depleting and high global warming refrigerants. Older compressor-based systems utilize environmentally harmful HFC refrigerants including R134a and R404A. Modern compressor-based systems now use a variety of natural refrigerants: R744 (carbon dioxide), R717 (ammonia), R290 (propane), R600a (Iso-Butane), and R1270 (propylene). Although they have their own complications, including flammability, these natural refrigerants are significantly better for the environment.
Comparing Cooling Technologies
Traditionally used in industrial laser applications, compressor-based refrigeration systems offer a high coefficient of performance (COP). For example, if they are cooling a heat load of 3 kW, a standard compressor-based refrigeration system typically requires around 1 kW of energy to provide the proper cooling, which is more efficient compared to thermoelectric cooling.
Compressor-based systems also tend to be smaller than alternative technologies like liquid-to-air heat exchangers, because they require less energy. Thermoelectric devices on the other hand are smaller, but they are less efficient. In addition, liquid-to-air heat exchangers do not cool below ambient temperatures like compressor-based and thermoelectric systems.
Central facility cooling systems used to cool the entire building have also been used for cooling industrial laser applications. However, these systems cannot guarantee a constant temperature and flow rate. It can also be difficult to satisfy all of the industrial cooling requirements with one large centrally controlled system.
Laird Thermal Systems Solution
The Nextreme™ Recirculating Chiller Platform from Laird Thermal Systems offers reliable and precise temperature control for industrial laser applications. Utilizing high-performance variable speed motors, it offers low noise operation and reduced energy consumption by up to 50% compared to conventional compressor-based systems. By using environmentally-friendly R513A refrigerant, the Nextreme™ Chiller delivers similar performance with half the Global Warming Potential (GWP) compared to traditional hydrofluorocarbons (HFC) refrigerants.
When it comes to temperature stability, the chiller platform achieves an accuracy of ±0.1°C and as the unit heats and cools fluid to maintain the thermal set point, it offers great flexibility. Industrial laser systems benefit greatly from the precise temperature control, ensuring optimum performance of the power source and laser optics. Featuring a LCD touchscreen display, the Nextreme™ Chiller Platform is designed with the end user in mind. It allows the user to control temperature setpoints, coolant type, flow and alarm settings while coolant level is easily monitored via the indicator window on the front panel.
For maximum uptime, the Nextreme™ Chiller features the optional “hot swappable” 5-micron water filter for filtering particulates from the coolant circuit, which means that there is no need to shut down the unit during maintenance. With no moving parts, an optical fluid level sensor offers improved reliability and increased uptime when compared to chillers that use mechanical float switches. The programmable alarm alerts the user when fluid level falls below acceptable operating conditions. To prevent damage to equipment in high pressure operating conditions, the chiller senses the supply fluid pressure and will alert users when low- or high-pressure limits have been exceeded.
The Nextreme™ Chiller Series is available in three standard cooling capacities including 1600W, 2800W and 4900W models. All these models can be configured to meet specific application requirements.
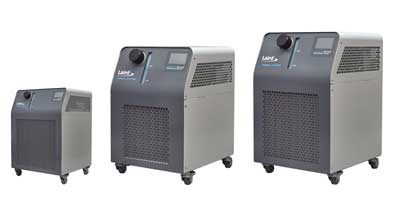
The Nextreme™ Chiller Platform is available in three different capacities, 1600W, 2800W and 4900W.
Conclusion
Properly cooling industrial laser systems is challenging, as power densities continue to increase while form factor requirements continue to shrink. However, today’s compressors are more efficient than a decade ago. Compact chiller systems offer a higher coefficient of performance that delivers efficient, low power consumption to maximize uptime and optimize performance in industrial laser systems. The versatile Nextreme™ Recirculating Chiller platform offers quiet operation in a smaller and lighter package compared to previous versions. The chiller platform provides higher efficiency and reliability than air-based heat exchangers and thermoelectric devices. This enables a more focused and improved laser performance for more precise cutting, welding, micro-machining, drilling and more.
More information on the Nextreme™ Chiller Platform can be found by visiting lairdthermal.com/nextreme-chiller
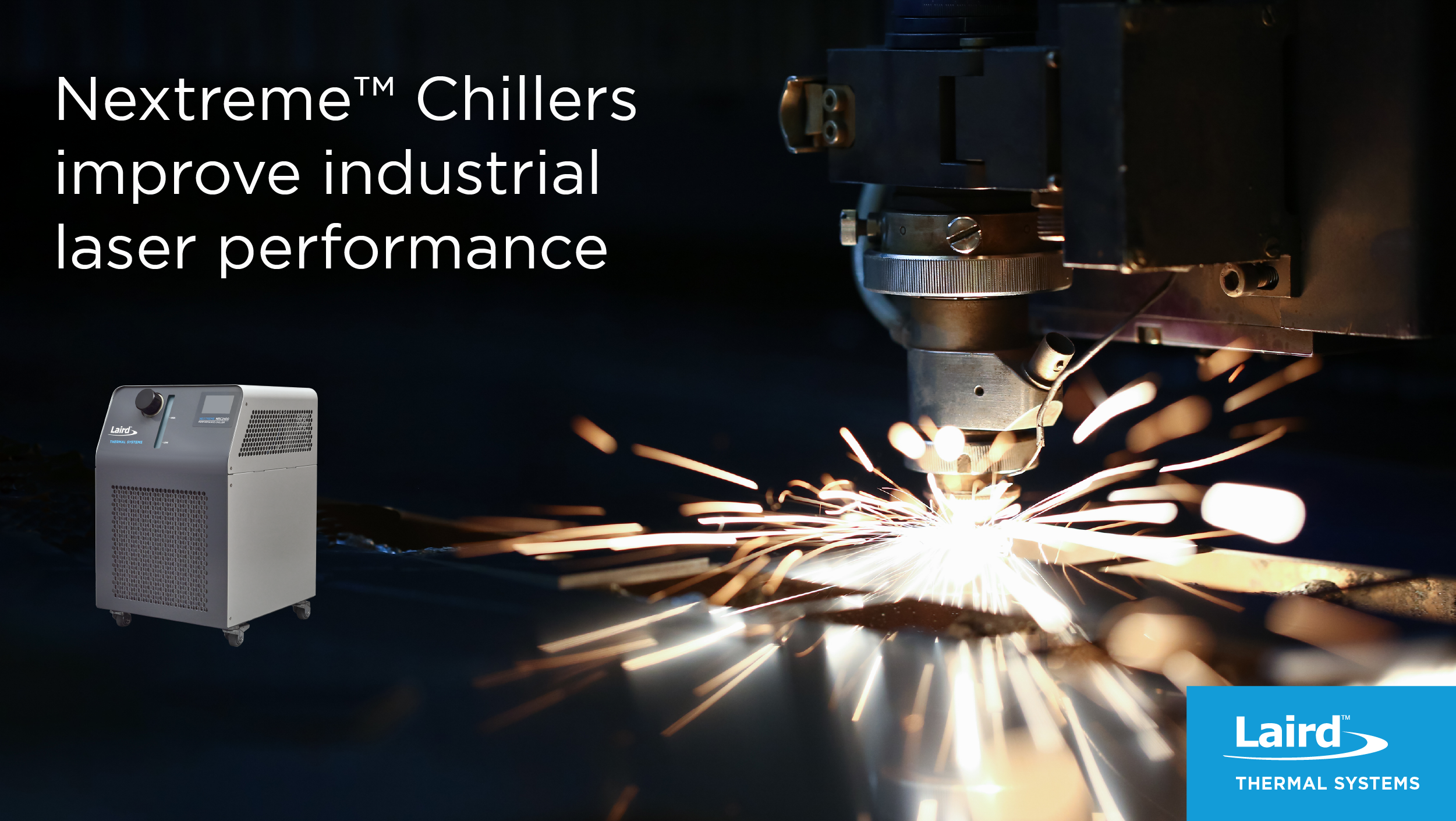