Introduction
Reagents are essential for laboratory and medical testing. Reagent materials are used to detect the presence or absence of a substance, or to test if a specific reaction occurs. Thermal control is vital to preserve reagent materials, which can degrade over time when stored at improper temperatures. When they are kept at room temperature, reagents may become contaminated by microbial growth, which affects test integrity. Reagents can also be negatively affected at low temperatures if they undergo multiple freeze-thaw cycles.
Given the high cost of many reagents, thermal control of reagent storage systems should be taken into consideration. Compressor-based refrigeration and freezer systems offer a high coefficient of performance (COP) to efficiently deliver precise temperature control below ambient. Technology advancements have eliminated many previous disadvantages of compressor-based systems including size, weight, reliability, eco-friendliness, and cost. Standard and custom compressor-based refrigeration systems are an ideal solution for thermal control of biological materials like reagents.
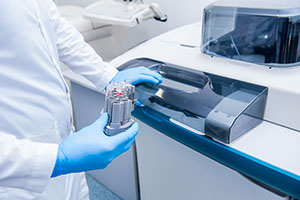
Temperature control is vital to preserve medical reagents.
Application Overview
Biological and chemical reagents are employed to identify and measure a target substance by laboratory and medical technicians. In biotechnology, reagents have been used to identify and manipulate chemical matter in cells. Reagents may be a compound or a mixture. In organic chemistry, most reagents are small organic molecules or inorganic compounds.
Whether a compound, mixture, or organic molecule, most reagents share a common characteristic – they are susceptible to heat and thermal cycles. Reagents have a narrow thermal window for storage and use, which requires precise temperature control. Biotechnology reagents are particularly affected by heat.
Precise thermal management below ambient increases the shelf life of reagents, reducing reagent replacement costs and ensuring the accuracy and reliability of laboratory or medical tests. Different reagents used in chemical and biological processes react differently to storage temperatures. Reagent storage systems have different requirements depending on the specific reagent and the storage time. These storage systems are generally classified into five types based on temperature range control:
Storage System | Temperature Range Control |
Cryogenic Freezer | -150°C to -190°C |
Ultra-low Freezer | -85°C |
Standard Freezer | -20°C |
Refrigerated | 2°C to 8°C |
Room Temperature | 15°C to 27°C |
In this application note, we will focus on compressor-based temperature control for reagent storage refrigerators.
Application Cooling Requirements
Refrigerator temperatures, which typically range from 2°C to 8°C, provide a short-term storage solution for frequently used biological reagents such as enzymes and antibodies. Within this temperature range, reagents tolerate minor temperature changes. However, some reagents are more sensitive and will start to break down after only a few of these minor temperature swings. Advanced storage refrigerators using compressor-based refrigeration systems are able to offer precise temperature control, accurate to within ±1°C.
Application Challenges
Precise temperature control is one of many designs challenges OEMs face when developing reagent storage systems. Size, weight and power (SWaP) requirements play a significant role in the design and manufacturing of reagent storage equipment. Other challenges include minimizing the operating noise level, managing the airflow within the cooling system, preventing condensation inside the chamber and activating temperature alarms if control is not properly maintained. Using eco-friendly, government and industry approved refrigerants is also vital for compressor-based systems to ensure future-proofing of the system.
Miniaturization of equipment to free up laboratory space is as prevalent as ever. This includes reducing the physical size of reagent storage equipment without reducing the storage capacity. This is often achieved by packing more reagents into a smaller space, which could result in a higher thermal load to the unit and a more obstructed path for chilled air to reach the reagents. To meet the required cooling capacity in a more compact form factor, refrigeration systems must have a high coefficient of performance and utlize components that will achieve the desired results. In order to increase performance while reducing power consumption and noise level, waste heat must be managed and dissipated efficiently.
The installation location and mounting orientation of the thermal management solution are critical when space is limited. Compressor-based refrigeration systems must mount vertically for proper operation. The mounting orientation plays a role in airflow as well. Paths for incoming and exhaust air must be considered to maximize the cooling performance.
In addition to providing precise temperature control, the thermal management system must also provide condensation protection. Moisture forms on cold surfaces as the temperature drops below the dew point. If this moisture seeps into the reagents, it can cause deterioration and ultimately poor test results. Using properly designed insulation materials and air flow paths can provide a cooling solution that limits the formation of condensation.
Many laboratories log the temperature inside the reagent storage chamber to keep record of the thermal conditions. More importantly, refrigeration systems feature alarms to alert technicans if the temperature diverges beyond the set temperature range. There are many government and industry accrediting bodies that have different criteria for evaluating the effectiveness of temperature monitoring; they all address and require certain basic elements that cover the form, frequency, and documentation of monitoring; the calibration of monitoring equipment; and staff training and competency in monitoring.
Faced with climate change, many governments, particularly those in Europe, continue to develop and update strict environmental regulations that ban the use of environmentally harmful refrigerants. Older compressor-based systems that utilized HFC refrigerants including R134a and R404A are becoming restricted in certain industries, and must now use natural refrigerants. Modern compressor-based refrigeration systems use a variety of natural refrigerants, including R744 (carbon dioxide), R717 (ammonia), R290 (propane), R600a (isobutane), and R1270 (propylene). However, the flammable nature of some natural refrigerants can make them hazardous to transport, and each one presents design challenges such as increased pressure, high toxicity, flammability, asphyxiation, and less efficient performance.
Refrigeration Systems
Modern compressor-based refrigeration systems meet the reagent storage chamber design requirements mentioned above. Compressor-based refrigeration systems, which are self-contained units that recirculate air to a predefined set-point temperature, allow for optimal temperature stabilization for more precise process control. Refrigeration systems have the ability to dissipate the large amount of heat generated in reagent storage systems.
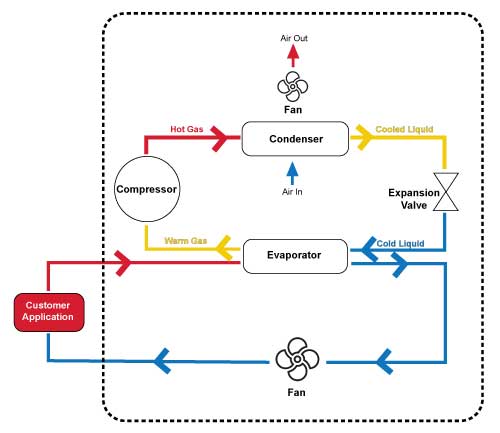
A conventional compressor-based refrigeration system contains four fundamental parts: the evaporator, compressor, condenser, and expansion device. The evaporator (cold section) is a heat exchanger where the refrigerant interfaces with the process fluid (air or liquid coolant in the case of a chiller) and evaporates (boils) from a liquid to a gas. During this change of state from liquid to gas, latent energy (heat) is absorbed at a constant refrigerant temperature. The compressor acts as the refrigerant pump and recompresses the gas. The condenser expels both the heat absorbed at the evaporator and the heat produced during compression into the ambient environment while the refrigerant changes phases again back into a liquid. The expansion device meters the amount of refrigerant flow while creating a reduction in refrigerant pressure to the point where it is ready to evaporate again.
Conventional compressor-based refrigeration systems can be either AC or DC powered. Today’s compressors are more efficient than a decade ago. Compact refrigeration systems offer a high coefficient of performance (COP) that ensures efficient, low power operation to maximize uptime and optimize performance. In fact, compressor systems offer a more desirable setpoint range than air-based heat exchangers and provide more rapid cooling and higher reliability. In steady-state operation at maximum designed heat loads, they can use 30% to 35% less power than a thermoelectric system.
A compressor-based system has several moving parts, which cycle constantly during operation. This contributes to noise and vibration, which can be detrimental to the system level electronics housed within the enclosure. However, modern compressor-based liquid cooling systems offer much quieter operation in smaller and lighter packages compared to previous versions.
When warm, moist air passes over the refrigeration coils of an refrigeration unit, condensation forms that drips from the coils. Moisture is often introduced when reagents are added or removed from the storage area. Thus condensation can form whenever additional moisture is introduced during system operation. Condensation also forms during normal operation when moist air is introduced into these refrigerated spaces. The compressor-based refrigeration systems, reagent storage area, and ducts are designed and installed so that gravity enables condensate to be collected in drains in these refrigerated spaces.
Compressor-based systems used for cooling electronics are typically designed for operation between 20°C and 55°C. This range is useful for most enclosure applications and operating environments. If heating is required, a separate heater and switching circuit must be used or if higher or lower temperatures are desired, additional design considerations must be given for operating in that range (refrigerant, hardware).
Laird Thermal Systems Solutions
Due to the increasing complexities of reagent storage systems, and the constant pressure to reduce product development cycle times, companies are relying on external, specialized thermal management expertise more often. Laird Thermal Systems has more than 45 years of experience in the design, manufacture and servicing of refrigeration and liquid cooling systems for various high-end markets.
While Laird Thermal Systems focuses on designing the optimal thermal solution, OEMs can focus on designing a better reagent storage system. All thermal systems are manufactured in an ISO 9001 and ISO 14001 certified facility and are built to meet the needs of strict process control requirements with heat loads up to 5000W. All parts are procured from strategic suppliers with a proven track record of suppling highly reliable components and offer strong design support for miniaturization and customization.
Laird Thermal Systems’ compressor-based refrigeration systems for reagent cooling utilize natural, eco-friendly R600a (isobutene) or R290 (propane) refrigerants that meet government and industry regulations. As refrigerant restriction laws continue to change, Laird Thermal Systems offers after sales service support to repair or replace units that have been in the field for more than two decades. Laird Thermal Systems can help customers with older units retrofit systems to meet government and industry refrigeration requirements.
Since there are many unique attributes that need to be ascertained from a reagent storage chamber, a custom cooling system configuration may be required to optimize performance and long-life operation. Laird Thermal Systems offers strong engineering design services with a global presence that supports onsite concept generation, thermal modeling, mechanical and electrical design and rapid prototyping. The company also offers validation test services to meet unique compliance standards for each medical industry.
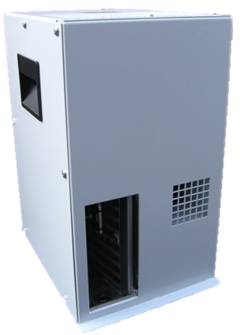
Laird Thermal Systems designs and manufactures compressor-based refrigeration systems for reagent cooling applications.
Conclusion
Thermal management of reagent storage systems is more challenging than ever. While power densities continue to increase, form factor requirements continue to shrink. The shelf life of a reagent can be greatly affected by temperature instability. In reagent storage chambers, compressor-based refrigeration systems offer the most efficient and reliable thermal control method. Laird Thermal Systems ensures precise thermal control for reagent storage equipment in a smaller package size with lower noise, environmental friendliness and lower total cost of ownership.
More information on custom compressor-based refrigeration systems, visit
www.lairdthermal.com/products/custom-solutions/liquid-cooling-systems-medical-diagnostics
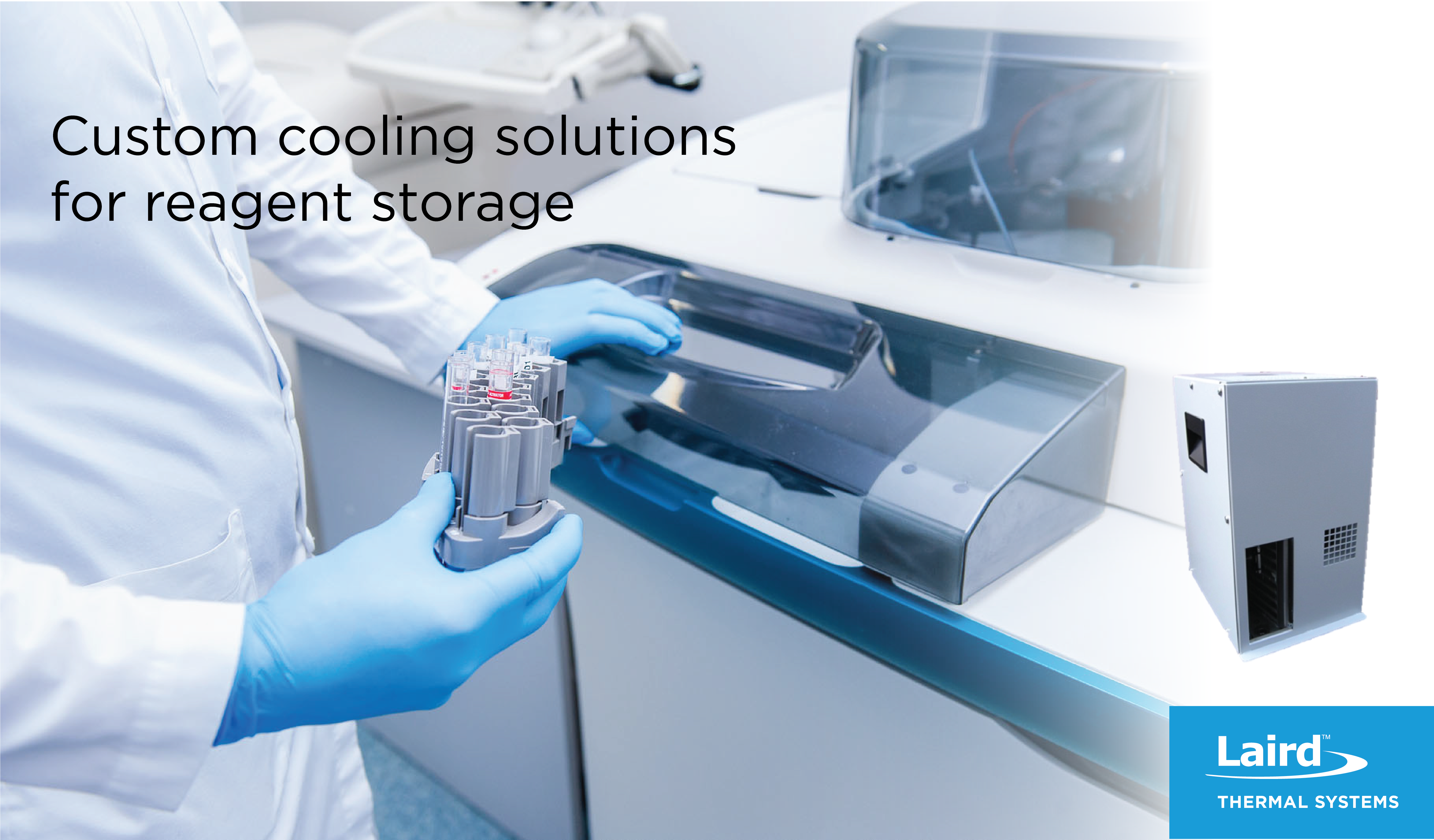