Thermoelectric Cooler Assemblies Solve a Lot of Thermal Management & Design Engineering Issues … with a lot of flexibility
Thermoelectric cooler assemblies, often referred to as Peltier Cooler assemblies are compact cooling units that control the temperature in a wide range of applications. With the ability to cool well below ambient, thermoelectric cooler assemblies protect electronics inside enclosures from outside contaminants, and limit moisture exposure from the outside environment. Offering precise temperature control, thermoelectric cooler assemblies are designed to meet the thermal management needs of many thermal management applications including enclosures, mobile base stations and cell towers, outdoor kiosks, beverage cooling, energy storage systems, medical diagnostic and analytical instrumentation, CMOS and imaging sensors, industrial and medical lasers, refrigerated centrifuges, incubator chambers and medical imaging systems.
OEM products can reach the market faster when the designer starts from a standard thermoelectric cooler assembly platform and modifies it as needed. Thermoelectric cooler assemblies offer several advantages over other cooling technologies like compressor-based systems. They can cool to well below ambient and offer precise temperature control, achieving ±0.01°C under steady-state conditions. They are also highly reliable with almost no maintenance and are mountable in any orientation. Compared to compressor-based systems, they are much lighter with a smaller footprint. In addition, new government restrictions of traditional and natural refrigerants central to traditional compressor-based systems make thermoelectrics a more advantageous thermal management solution.
Working with a manufacturer that specializes in thermoelectric cooler assemblies, normally results in a product that is optimized for performance, packaged in a smaller footprint and has a lower power requirement
Standard thermoelectric cooler assemblies use heat transfer mechanisms designed to absorb and dissipate heat by convection, conduction, or through liquid heat exchangers. Depending on the application, having these heat transfer solutions available to choose from shortens the design cycle and shortens the time to finding an optimized solution. Here are the heat transfer mechanisms available for absorbing and dissipating heat.
Air-to-Air assemblies offer dependable, compact performance by cooling objects via convection. Heat inside the chamber is absorbed by the cold side heat exchanger. The thermoelectric coolers pump heat from the cold side heat exchanger and dissipate through the hot side heat exchanger to the outside environment. The internal air circulation from the cold side fan helps minimize the temperature gradient within the enclosure. This configuration is commonly used in sample storage chambers for medical and analytical instrumentation, electronic enclosures, and compartment storage for food and beverage applications.
Air-to-Air TEAs Options from our SuperCool X Series
![]() |
![]() |
Air-to-Air TEAs Select Options from the PowerCool Series
![]() |
![]() |
Direct-to-Air assemblies offer dependable, compact performance by cooling objects via conduction. Heat is absorbed through a cold plate and thermoelectric cooler pumps heat thru a hot side heat exchanger and into the ambient environment. The internal cold plate allows the chamber to be completely sealed, which aids in containing bio-hazardous liquids and minimizing contamination. It also saves space in small chambers that cannot accommodate a cold side heat exchanger. This configuration is commonly used in smaller sample storage chambers for medical and analytical instrumentation, spot cooling for laser systems or sensitive optical electronics used in the industrial and telecom markets.
Direct-to-Air TEA Options from SuperCool X Series
![]() |
![]() |
Direct-to-Air TEA Select Options from PowerCool Series
![]() |
![]() |
Liquid-to-Air assemblies cool or heat a coolant in a re-circulating liquid circuit. Heat is absorbed by an external liquid heat exchanger and moved through a liquid circuit by an external pump. Heat is absorbed by the cold side liquid heat exchanger then pumped by thermoelectric coolers thru the hot side heat exchanger and dissipated to ambient environment. This configuration is ideal for spot cooling where localization of a thermoelectric assembly is not possible due to space constraints. Common applications are imaging systems, medical diagnostics, and laser systems in the industrial, semiconductor and medical markets.
Liquid-to-Air TEA Examples from SuperCool X Series
![]() |
![]() |
![]() |
Direct – Liquid assemblies cool or heat devices or chambers via liquid to transfer heat. The advantage of this configuration is that there is more cooling capacity of the TEMs utilized because liquid heat exchangers are more efficient at dissipating heat than conventional heat sink fan mechanisms.
Liquid – Liquid assemblies cool or heat liquids as they pass through a heat exchanger. They are ideal for controlling the temperature of process fluids in a liquid circuit and utilizes available process water as a cooling mechanism commonly found in many semiconductor applications.
Engineers must now consider thermal management early in the product design process. Simple thermal management solutions, such as adding a fan or heat sink, are no longer typically viable to meet required performance and reliability specifications. A standard thermoelectric cooler assembly allows the designer to start with a basic set of building blocks that mate fans and thermoelectric coolers to heat exchangers. Laird Thermal Systems has conducted two decades worth of design and validation testing on various combinations of thermal components to optimize cooling power and efficiency at various heat loads. This results in engineers saving time with redesign and validation testing a thermoelectric cooler assembly that has already been perfected by Laird Thermal Systems.
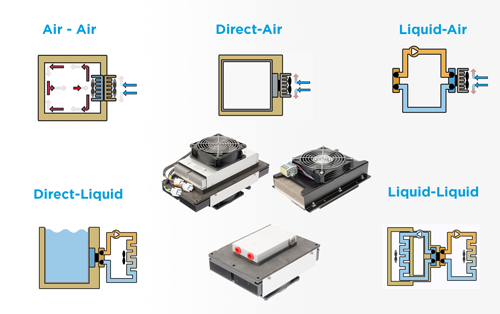
Related Products
Stay tuned for updates on thermal management industry regulations, new product releases, and innovative temperature control approaches with
LTS Thermal Solutions Spotlight:
Categories
Blog Date