Liquid Cooling Systems
Laird Thermal Systems provides robust liquid cooling solutions (LCS) for many of the temperature critical applications found in the medical, analytical, industrial and semiconductor markets. With cooling capabilities from 100 watts to 25K watts and beyond, our LCS systems are designed to maximize temperature stabilization at above, below or equal to ambient temperature. Service life expectations can exceed more than 20 years in the field.
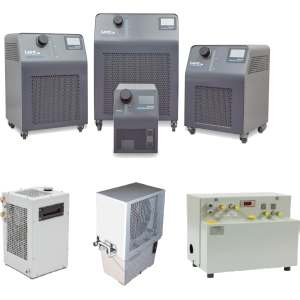
About Liquid Cooling Systems
In today’s complex operating environment, liquid cooling systems are required to dissipate a large amount of heat in a densely packed electronic environment. Maximum operational life is required to keep system maintenance and repair down time to a minimum. Temperature stabilization has especially become critical, as next generation systems require more precise temperature control. Liquid cooling systems are self-contained units that recirculate a coolant to a predefined temperature set point. There are two types of liquid cooling solutions.
- Liquid heat exchanger systems cool the coolant in a liquid circuit to ambient temperature. This system consists of a pump to circulate coolant, a liquid heat exchanger to dissipate heat, and a liquid circuit to transfer coolant from the heat source to the liquid cooling system.
- Liquid Chillers (recirculating chillers) encompass a compressor system instead of a liquid heat exchanger assembly. It is used to cool the coolant to well below ambient and dissipate heat to the outside environment.
Additional features can easily be included to add temperature control, variable flow control, bypass control, coolant filtration and electronics in order to meet unique attribute requirements.
Laird Thermal Systems’ liquid cooling systems are used in a wide range of healthcare diagnostics & treatment, industrial instrumentation and semiconductor fabrication applications. While Laird Thermal Systems focuses on designing the optimal liquid cooling solution, customers can focus on designing a better end instrument. All products are manufactured in an ISO 9001 and ISO 14001 certified facility and are built to meet the needs of strict process control requirements found in many of the medical, industrial, and semiconductor industries. All parts are procured from strategic suppliers with a proven track record of supplying highly reliable components, and offer strong design support for customization. Laird Thermal Systems also offers after sales service support to repair or replace units that have been in the field for more than two decades.
Liquid cooling systems are unique to the thermal management market in that they use a coolant to transfer heat. Liquid cooling systems have several advantages over conventional air-cooled systems, such as:
- High heat pumping capacity
- High heat flux density
- Heat routing
- Rapid cool down
- Lower noise
Turn-key Capabilities
The optimal liquid cooling solution is often a custom configuration. Laird Thermal Systems has more than 45 years of experience in the design, manufacture and servicing of custom liquid cooling systems for various high-end markets. Our experienced engineering team designs cooling systems that are compatible with water, water glycol, transformer oil, or various corrosion prohibitors. Liquid cooling systems can also be quite complex and require the temperature control of multiple liquid circuits or multiple pressure drop settings in order to accommodate low and high-pressure conditions. Laird Thermal Systems has experience designing both systems, and can integrate many unique attributes into a liquid cooling system, such as:
- Cooling capacity (up to 200 KW)
- Variable pump capacity
- Thermal control of multiple liquid circuits
- Coolant filtration
- Variable flow control
- PID temperature control
- High temperature stability
- High Coefficient of Performance (COP)
- Durability by hot gas bypass control
- CFC-free refrigerants
- Stainless steel heat exchanger
- High operational temperatures
- Flow monitoring
- Level switching
- Fault signal potential-free
- Maximum pressure limit
- Custom input/output fittings and housing configuration