Infrared Sensors are electronic devices that use infrared radiation to perform a variety of functions across a wide range of applications from consumer electronics to industrial automation to medical and scientific research to military and aerospace.
IR Sensors can be categorized as either thermal or quantum (photon) detectors. Thermal detectors typically do not require cooling as they often operate in room-temperature environments. In contrast, quantum detectors often require cooling to function optimally. These detectors are sensitive to thermal noise and need to be cooled well below ambient temperatures (typically between -20°C and -80°C) to reduce dark current and enhance the signal-to-noise ratio. Lower temperatures allow for the detection of lower energy IR photons, which is especially important for short-wave IR (SWIR) applications requiring high sensitivity and precision. Although SWIR typically falls in the short-wave spectral range, cooling is also crucial for mid- and long-wave IR sensors to minimize thermal noise that can distort image quality. This is particularly important in applications like surveillance and thermal imaging, where high image resolution and accuracy are critical. Cooling these types of sensors helps minimize thermal noise which can distort image quality.
Thermal or Quantum Detector?
There are various types of IR sensors, each suited to specific applications and desired outcomes. As mentioned above, they can be classified as a thermal detector (T) or a quantum detector (Q) or both.
- Active IR sensors (T) contain an emitter and receiver, emitting IR radiation and detecting the reflected signal for use in proximity sensing and detecting obstacles.
- Passive IR sensors (T) only detect IR radiation (do not emit it) for use in detecting changes in IR levels from moving objects such as motion detection in security systems and automatic lighting.
- Reflective IR sensors (T) emit IR light and use a phototransistor to detect reflected light used for proximity and distance measurement
- Transmissive IR Sensors (T) have an IR emitter and receiver separated by a gap and detect when an object interrupts the IR beam as used in counters and break-beam sensors
- IR Imaging Sensors (T or Q) create thermal images by detecting IR radiation used in thermal cameras and night vision devices
- IR Spectroscopy Sensors (T or Q) analyze materials by measuring their IR absorption, used in chemical analysis and material identification
- IR Proximity Sensors (T) detect nearby objects without physical contact and are used in touchless interfaces and robotics
IR Sensor Applications Needing Active Cooling
Several types of IR sensors require cooling to operate effectively, particularly those used in high-performance applications. In short-wave infrared (SWIR) systems, thermoelectric coolers (TECs) are commonly used to lower detector temperatures, which helps:
- Reduce thermal noise and dark current
- Improve the detection of low-energy IR photons
- Boost sensor sensitivity and image quality
While mid-wave (MWIR) and long-wave infrared (LWIR) systems may sometimes require more extreme cooling solutions (like cryocoolers), quantum IR detectors, such as InGaAs or HgCdTe (MCT), which are also used in MWIR and LWIR, often utilize TEC cooling to achieve optimal performance. But TECs are especially effective for SWIR applications, providing a reliable, efficient solution for maintaining the necessary operating conditions without the complexity and higher power demands of cryocoolers.
Listed below are key applications that often utilize active cooling for IR sensors:
- High-Performance Imaging Systems Infrared Range (IR) sensors measure distance and are used in a variety of applications, including temperature sensing, video surveillance and motion detection.
![]() |
![]() |
- Military and Defense: Cooled IR detectors are extensively used in thermal imaging and military applications for night vision, target acquisition, and missile guidance systems. These systems often require high sensitivity and resolution, which is achieved by cooling the IR sensors to reduce thermal noise.
Image courtesy of FLIR
- Industrial and Environmental Monitoring: In industrial settings, cooled IR detectors are employed for non-contact temperature measurements and thermal imaging. They are also used for gas analysis and pollution control, where detecting specific gas emissions requires high sensitivity to longer IR wavelengths.
- Medical Imaging: In the medical field, cooled IR sensors are used in thermography to detect subtle temperature variations in the human body, which can be indicative of underlying medical conditions. The cooling helps in achieving the precision needed for accurate diagnostics used in breast cancer detection, diabetic neuropathy, vascular imaging, and rheumatology
- Environmental Monitoring and Gas Detection: IR sensors detect gases by measuring the absorption of infrared light at specific wavelengths characteristic of different gas molecules. IR sensors are preferred due to their accuracy, reliability, and versatility across various applications, particularly in challenging environments where safety is paramount.
- In spectroscopy, IR sensors are essential for identifying and quantifying chemical compounds based on their unique absorption spectra. By detecting the specific wavelengths of IR radiation absorbed by different molecular bonds, these sensors enable detailed analysis of materials in various phases—solids, liquids, and gases.
Common Challenges in Cooling IR Sensors
Cooling infrared (IR) sensors is crucial for ensuring optimal performance and reliability. However, several challenges must be addressed:
- Thermal Noise Management: Excess heat increases thermal noise, negatively impacting the signal-to-noise ratio (SNR) and sensor sensitivity. Effective cooling, particularly through thermoelectric coolers (TECs), is necessary to minimize thermal noise and enhance performance.
- Complexity and Cost: The implementation of cooling systems adds complexity and cost to the overall design. Designers must balance the cooling solution's cost against the performance benefits it provides, especially in cost-sensitive applications.
- Size Constraints: IR sensors are often housed in increasingly smaller packages, such as miniature TO cans, sometimes fitting into footprints smaller than 9 x 9 mm. This requires cooling solutions that also shrink in size, which can compromise performance. Miniaturization requires precision handling during manufacturing, particularly in material preparation and soldering.
- Material Cleanliness: Smaller components typically need to be cleaned thoroughly which helps prevent contamination. When contaminants, such as dust or particles, are present on the thermoelectric cooler (TEC), they can lead to significant issues, especially in vacuum-sealed optoelectronic packages. Ensuring that these sensors remain uncontaminated not only protects their functionality but also enhances overall system reliability and longevity.
- Outgassing Considerations: Outgassing occurs when volatile compounds are released from materials, such as thermal epoxy, and can contaminate sensitive optical components, degrading sensor performance. In high-precision IR sensors, direct soldering to the optical package is the preferred method, as it not only eliminates outgassing but also enhances heat dissipation, improving overall thermal efficiency and sensor reliability.
- Maximized Efficiency: IR sensors, particularly in portable handheld devices face challenges related to their power consumption and the need for high efficiency. Maximizing efficiency is essential to extend battery life, as lower power consumption ensures longer operational times. TECs can enhance sensor performance while minimizing energy use, crucial for maintaining optimal function in varying conditions without rapidly depleting the battery.
- Environmental Sensitivity: Cooling systems may be affected by environmental factors such as humidity and temperature fluctuations. These conditions can influence their performance and reliability, making careful consideration of the operating environment essential.
- Specialized Cooling Solutions: Given the specific requirements of IR sensors, cooling solutions should be optimized for their unique operating environments.
By understanding and addressing these challenges, developers can enhance the effectiveness of cooling solutions for IR sensors, ensuring they perform optimally across various applications.
Cooling IR Sensors
Thermoelectric cooling is the most common method for cooling IR sensors in these applications. Thermoelectric coolers (TECs) can:
- reduce dark current which reduces thermally generated charge carriers, lowering the dark current. This improves the signal-to-noise ratio (SNR) and overall detector sensitivity
- provide precise temperature control to within 0.1°C, ensuring stable detector performance
- allows detectors to operate effectively at longer infrared wavelengths by reducing thermal noise in small-bandgap semiconductor materials
- be easily integrated into compact optical systems, allowing for efficient cooling of small detector chips to temperatures below -70°C
- extend lifetime by reducing thermal stress on the detector, thereby extending the operational lifetime of the device
- improved performance for imaging applications
- achieve temperature stabilization allowing for more effective non-uniformity correction (NUC) to normalize pixel offsets
- expand the spectral range by enabling the use of IR detectors across various spectral bands, including near-infrared (NIR) and shortwave infrared (SWIR)
- operate with low electrical noise due to their DC operation
- offer long operational lifetimes (>10 years) as solid-state devices
For extremely high-performance applications requiring temperatures below 180K, cryogenic cooling methods will be necessary.
Following Laird Thermal Systems thermoelectric coolers provide deep cooling for IR sensors to ensure high-resolution images and the capturing of maximum light spectrum in the infrared range.
Cooling Solutions
The compact OptoTEC™ MSX Series is used to deliver deep cooling to well below ambient in high-performance imaging sensing applications including IR Detectors. The multistage TECs offer micro footprints on the cold side down to 2.0 x 4.0 mm with height thicknesses down to:
- 3.3 mm for 2 stage
- 3.8 mm for 3 stage
- 4.9 mm for 4 stage
The highly customized applications for this product series require unique ceramic substrate materials and thicknesses. Two solder constructions are available to accommodate reflow temperatures up to 230°C or 280ºC. MSX is offered in Au-plated pads or uninsulated lead wires for lead attachment.
Offering up to 10 Watts of cooling power in an extremely small footprint, the OptoTEC™ OTX Series is ideal for IR sensor applications with tight geometric space constraints.
To learn more, read our application note on Advanced Thermoelectric Cooling for Optoelectronics.
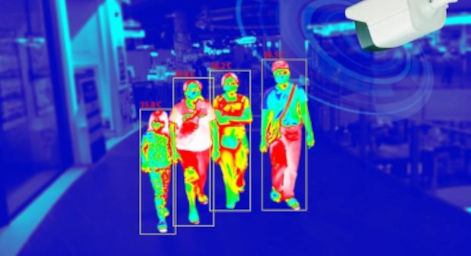
Related Products
Stay tuned for updates on thermal management industry regulations, new product releases, and innovative temperature control approaches with
LTS Thermal Solutions Spotlight:
Categories
Blog Date