Introduction
Lasers come in many different sizes and power levels. High power lasers are commonly used for brazing, metal cutting, deep metal welds and metal cleaning, while low power lasers can be used for printing & marking, soldering, plastic welding and laser powder remelting. For all laser technologies, OEMs seek advanced cooling of the power source and the laser optics to maintain peak performance and long life operation. High power lasers typically require a more robust liquid cooling solution (see application note on cooling high-power lasers) while low power lasers can utilize a thermoelectric-based recirculating chiller. In this application note, we will focus on cooling techniques for low-power laser equipment.
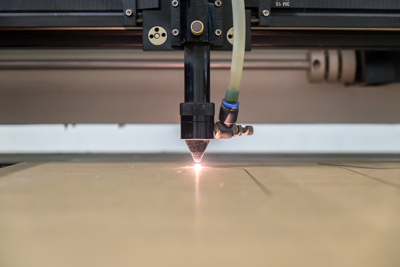
Industrial laser applications require active cooling to maintain peak performance.
Application Background
For low power lasers, such as small helium-neon or argon-ion lasers, passive cooling techniques can be sufficient. Passive heat dissipation utilizes a heat sink to maximize the natural convection of heat transfer with air. Some passive cooling laser systems will also feature a cooling fan to increase convection with air to dissipate heat more quickly. However, a passive system does not always provide adequate heat dissipation to keep sensitive electronics cool.
Industrial laser systems larger than 10 Watts typically require some kind of active cooling. Small gas lasers and many solid-state lasers often feature a closed-loop heat exchanger cooling system. The design of a closed loop cooling system can be simple. An effective cooling loop system circulates coolant to the laser, absorbs heat and then dissipates it thru liquid heat exchangers in such a manner that the coolant does not come into direct contact with the environment at any time. The coolant remains clean, uncontaminated, and does not cause fouling, scaling, corrosion or erosion of heat transfer surfaces.
Compressor-based refrigeration systems have long been used to cool laser systems. However, traditional laser design challenges and recent technology advancements have led to the implementation of thermoelectric-based chillers for spot cooling of low power lasers and optical components.
Laser Design Challenges
Temperature stability is critical for laser systems. However, lasers inherently generate heat, particularly in the laser gain medium due to the unfinished conversion of optical pump power into optical output power. In diode-pumped lasers, the use of laser diodes also generates waste heat. In low-power laser systems, waste heat typically ranges from tens of watts up to several hundreds of watts, which must be efficiently dissipated away from the sensitive laser components. A thermoelectric recirculating chiller must provide precise temperature control below ambient temperatures and condensation protection to maintain peak performance.
Space Constraints
Miniaturization demands have increased as more electronics are packaged into smaller form factors. Lasers can have high heat flux densities and be buried in the heart of a laser system. Waste heat generated by the laser must be routed out of the laser system and dissipated efficiently without elevating temperature of surrounding components. Dissipating heat from laser with an air heat exchanger will increase the temperature of surrounding electronics. However, using localized spot cooling will provide the benefit of capturing heat generated by the laser and route it thru a liquid circuit to a recirculating chiller located outside the laser system. This allows for proper heat dissipation to surrounding environment while maintaining a stable temperature in the laser system.
Temperature Control
Depending on the type of materials used, laser optics need to be kept at a nominal temperature between 20 to 35⁰C with a temperature stability of ±0.5°C. Precise temperature control eliminates laser power fluctuations, enabling the laser to operate at a stable wavelength for peak beam performance and quality. Cooling key optoelectronic components helps extend operation life, maximizes equipment uptime and lowers total cost of ownership by increasing the mean time between failures (MTBF) of optoelectronic components.
Noise
Equipment cooling units can play a significant role in the decibel level on a manufacturing floor. Cooling systems should be designed to minimize noise and vibration during operation. Noisy compressor-based systems may result in higher cooling capacity, but can be distracting to operators. Thermoelectric-based recirculating chillers use smaller fans pushing less airflow and generally operate at lower noise than larger compressor based systems. Fan speed can also be controlled to reduce noise, but this will impact cooling performance.
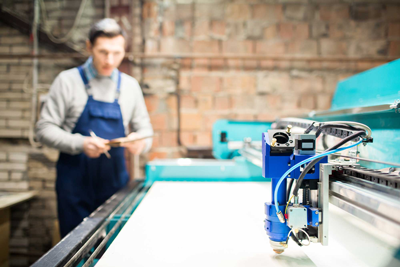
Cooling solutions of modern laser equipment must offer low noise operation without impacting cooling performance.
Portability
Today’s advanced laser system cooling solutions are designed for portability so that they can be used to cool multiple pieces of equipment in a facility. Traditional compressor-based cooling solutions are often bulky and heavy and can weight in excess of 50 kg’s, which makes them challenging to move. Smaller recirculating chiller solutions using thermoelectric-based technology are much lighter, ranging from 10 to 20 kg’s and can be moved with ease.
Condensation
It is important to protect laser components from condensation. When cooling below ambient, any surface that goes below dew point will condense and build up moisture quite quickly. Even for applications where the set point temperature is at 20⁰C, components in the recirculating chiller can be below 15°C to maintain that set point temperature. This will most likely be below dew point. Sealing all surfaces that go below dew point is critical to minimize moisture. This is often done by insulating hoses and surfaces with a closed cell foam or other type of insulation that does not absorb moisture and has good thermal insulating properties.
Environmental Regulations
Government restrictions of natural and traditional refrigerants central to compressor-based systems are motivating manufacturers to look for alternative environmentally friendly options. Because thermoelectric technology does not make use any CFC refrigerants, OEM’s are considering thermoelectric-based recirculating chillers as a substitute technology to traditional compressor-based systems.
Solutions
Recirculating chillers are a better option than passive solutions such as heat sink and fan or ambient liquid cooling systems because they can cool below ambient temperatures. Passive cooling solutions operate at a few degrees above ambient and may not provide enough cooling to keep the laser system stable and assure long life operation of critical components. A liquid cooling system is more efficient than an air cooling system at routing heat out of the laser system, minimizing the temperature increase of critical components.
Thermoelectric- or Peltier- based recirculating chillers are becoming more popular due to their inherent high reliability, minimal maintenance and environmental friendliness when compared to traditional compressor-based recirculating chillers. In addition, a recirculating chiller system that uses thermoelectric coolers offer more precise temperature control because thermoelectric coolers have the ability to both heat and cool.
In the below diagram a thermoelectric recirculating chiller is connected to the liquid circuit of a laser system. The type of coolant selected is important as water is most efficient with heat transfer, but can build up bacteria over time if not maintained. Pure water is also not ideal at temperatures approaching freezing. Adding an ethynol glycol water mixture of 10% to 30% will help minimize algae build up over time and assure long life operation. Higher concentrations of glycol are recommended for temperatures below freezing.
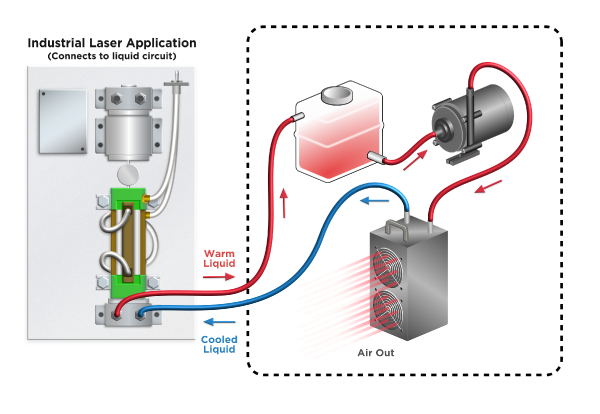
Thermoelectric recirculating chiller connected to the liquid circuit of an industrial laser system.
Semi closed systems help minimize air from getting into the system, which reduces algae growth and prevents coolant from evaporating requiring less refilling of liquid circuit. Larger reservoir tanks are recommended to reduce refilling of coolant during operation and allows for better temperature stability. At initial installation it is important to run unit in pump mode to circulate coolant prior to cooling to remove air bubbles.
Laird Thermal Systems Solution
The Nextreme™ NRC400 is a next generation benchtop recirculating chiller that combines advanced thermoelectric cooling with high performance heat exchanger technology. The compact unit utilizes thermoelectric coolers with advanced thermoelectric materials to achieve 400 Watts of cooling power, while offering precise temperature control stability to within ±0.05°C under steady state conditions.
Compared to previous models, the NRC400 has a higher coefficient of performance (COP) and a quieter operation. Because the recirculating chiller utilizes solid-state thermoelectric coolers, the NRC400 cooling system has few moving components resulting in less down time for maintenance requirements.
The portable NRC400 weighs only 21 kg, which is significantly lighter and smaller than conventional compressor-based cooling systems. The unit is a semi-closed system featuring a large reservoir tank requiring less refilling during operation and users can easily input temperature setpoints and alarms via the touchscreen display.
The environmentally-friendly NRC400 offers stress free environmental compliance to government regulations as no harmful CFC’s are used. Units operate on a universal power supply from 115V to 230V making it easy to source one part number globally.
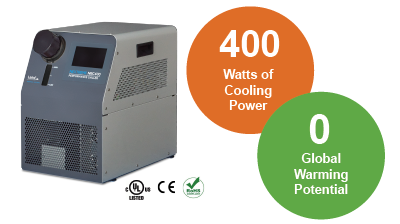
Conclusion
Processing and manufacturing industries are looking for ways to reduce costs while increasing throughput and quality. Compressor-based refrigeration systems have long been used to cool laser systems. However, technology advancements have led manufacturers to implement thermoelectric-based chillers providing more reliable and precise cooling of critical laser systems that increases portability and uptime. The NRC400 from Laird Thermal Systems is a next generation recirculating chiller offering OEMs a more sophisticated cooling system. By utilizing premium thermoelectric cooler technology, the NRC400 delivers improved temperature stability, higher COP and quieter operation than previous models.
More information on the NRC400 can be found by visiting https://www.lairdthermal.com/nextreme-nrc400
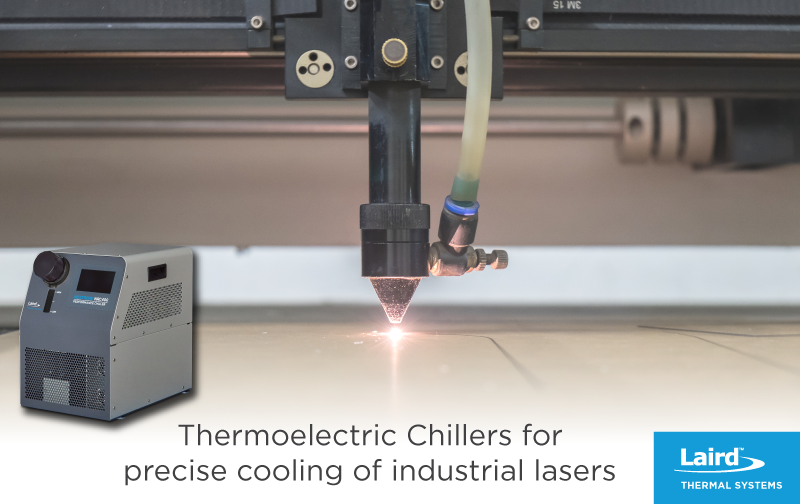