Introduction
Supporting the imaging needs of the multifaceted life science and biotechnology research industries, modern microscopy equipment offers magnification, resolution, and contrast for visualization, measurement and analysis of microstructures. Advancements in microscopes leverage visible and nonvisible light to provide high-quality images of cells. There are four types of microscopy: optical, electron, scanning probe microscopy, and the developing field of X-ray microscopy. All four types of microscope technologies require precise temperature regulation of heat-sensitive electronics to ensure proper, long-term operation of the microscope. OEMs implement thermal management systems that cool the digital cameras used for image creation to improve image quality. In this application note, we will be focusing on cooling requirements for optical microscopes (read our electronic microscope app note here).
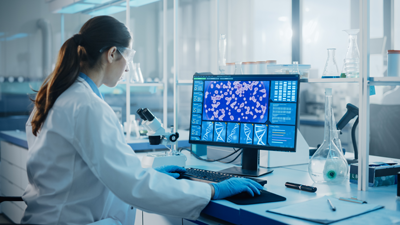
Modern microscopy equipment provide high-resolution images that allows for detailed measurements and analysis of microstructures.
Application Overview
Optical or light microscopy involves transmitting visible light through, or reflected from, a sample. Depending on the design of the microscope, light travels through a single lens or multiple lenses to enable a magnified view of the sample. The resulting image can be detected directly by the eye, imaged on a photographic plate, or captured digitally.
There are many optical microscope technologies, including brightfield microscopes, darkfield microscopes, phase-contrast microscopes, differential interference contrast microscopes, fluorescence microscopes, confocal scanning laser microscopes, and two-photon microscopes. Confocal microscopes, for example, use a laser to scan multiple z-planes to produce numerous two-dimensional, high-resolution images at various depths that can be constructed into a three-dimensional image by a computer, making this useful for examining thick specimens such as biofilms. In addition, modern digital microscopes use a CCD (charge-coupled device) or CMOS (complementary metal-oxide semiconductor) sensor-based camera to focus on the sample, displaying the resulting image on a digital screen. These various types of light microscopes can be used to complement each other in diagnostics and research.
Application Challenges
Digital microscopes utilizing a CCD or CMOS-based camera require precise temperature stability. CCD and CMOS image resolution degrades as temperature increases. Depending on the design, the microscope may contain several imaging sensors and field programmable gate array (FPGA) semiconductors to enhance resolution and capabilities. For example, new digital microscopes are able to generate high-quality 3D images. The internal electrical power source for more intricate 3D camera systems can generate upwards of 60W during use. The camera system and FPGAs must be efficiently cooled to maximize image resolution and rendering. Depending on the type of microscope, sensor temperatures of 18⁰C or lower could be required to allow for long exposures.
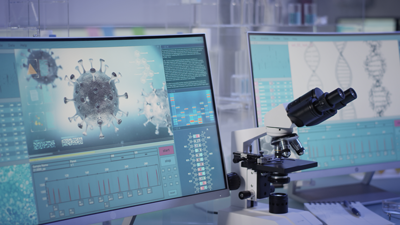
Digital microscopes require precise temperature control to deliver high resolution images.
No matter the type of light microscope, temperature stability is required for the proper performance and long-term operation of sensitive optoelectronic components. For example, lasers used in the confocal scanning laser microscope, inherently generates heat during operation. The majority of heat is generated in the laser gain medium due to the unfinished conversion of optical pump power into optical output power. In diode-pumped lasers, the use of laser diodes also generates heat, elevating temperatures. In these small laser systems, the amount of waste heat generated typically ranges from tens of watts up to hundreds of watts. To achieve optimal operating temperature, refrigeration systems are required to cool below ambient temperatures. This isn’t possible with passive cooling technologies like liquid heat exchangers that cool slightly above ambient.
Space Constraints
The miniaturization of camera systems can increase the heat flux density as more optoelectronics are packed into smaller form factors. Dissipating heat away from the imaging sensor with air-based heat exchangers will raise the temperature of surrounding electronics. By using a recirculating chiller, waste heat can be routed out more efficiently and dissipated into the surrounding environment.
Temperature Fluctuations
Sensitive camera optoelectronic components need to be kept below room temperature with a temperature stability of ±0.5°C or better. Precise temperature control is needed to keep the imaging sensor stable to maintain high image resolution. Cooling laser optics and key components also helps maximize equipment uptime, reduce maintenance and lower the total cost of ownership by increasing the mean time between failures (MTBF).
Noise & Vibration
In addition to precise cooling, the refrigeration system must continuously deliver a steady flow of coolant thru the liquid circuit with minimal pulsation. Vibrations from pump flow can distort microscope imaging resolution, creating noise in the image.
OEMs are also tasked with integrating cooling systems providing quiet operation (both lower noise and vibration). Large compressor-based systems tend to vibrate and are typically noisy. This can be distracting to an operator over an extended period of time. Thermoelectric-based chillers are designed with smaller fans and pumps providing lower noise and vibration.
Condensation
It is also important to protect optoelectronics within a microscope against condensation. For most applications the set point temperature is near room temperature. However, the cold side of the thermoelectric cooler can be at 10⁰C or lower to maintain that set point temperature. This will be below the dew point temperature and cause moisture in the air to condense. Sealing the perimeter of the thermoelectric cooler with RTV is not sufficient. It is recommended to have a second insulation barrier to protect the thermoelectric cooler cavity. All surfaces that go below dew point will require some type of insulation to keep moisture from condensing on those surfaces. This is usually a close cell foam or other type of insulation that does not absorb moisture and has good thermal insulating properties.
Environmental Regulations
Environmental regulation developments continue to phase out the use of destructive refrigerants tied to ozone depletion and global warming. Older compressor-based systems utilize environmentally harmful HFC refrigerants including R134a and R404A. Modern compressor-based systems now use a variety of natural refrigerants: R744 (carbon dioxide), R717 (ammonia), R290 (propane), R600a (Iso-Butane), and R1270 (propylene). Although they have their own complications, including flammability, these natural refrigerants are significantly better for the environment.
Solutions
With the ability to cool to well below ambient, thermoelectric recirculating chillers are a better option than passive solutions such as heat sinks and fans or ambient liquid cooling systems. Thermoelectric-based recirculating chillers are compact and have few moving parts. This offers high reliability with minimal maintenance throughout the product lifetime. Thermoelectrics are able to achieve very precise temperature control that is ideal for spot cooling applications in digital microscopes.
This illustration shows how a thermoelectric chiller pumps heat from an optical microscope imaging system down to 18ºC, while room temperature may fluctuate between 20 and 30ºC. Heat from the camera system is absorbed by the liquid coolant and flows to a reservoir tank by a pump.
The pump pushes the coolant thru the Liquid-to-Air thermoelectric engine, which then cools the temperature of the coolant circuit while exhausting waste heat into the ambient environment. The coolant then flows back to the camera system at a set point temperature where the cold plate is mounted. The system is semi-closed which makes it difficult for air to seep into the liquid circuit, reducing algae growth. An ethanol glycol water mixture is typically used as coolant to prevent algae growth from building up over time. The recirculating chiller can be designed to cool multiple critical optoelectronic components in series beyond the microscope’s camera system, such as a detector and/or FPGA’s.
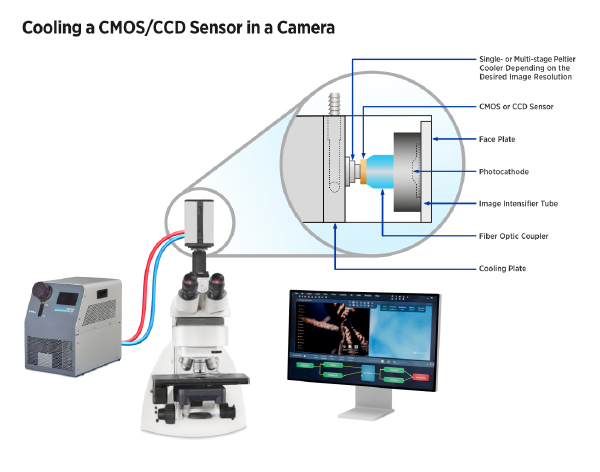
NRC400 Thermoelectric chiller cools optical microscope imaging system.
Integrated inside the camera is a thermoelectric cooler that is soldered to the cold plate and cools the CCD or CMOS sensor housing down further to -20 or -30ºC depending on the imaging resolution required. The combination of a recirculating chiller and thermoelectric cooler keeps thermal noise down and maximizes image resolution.
Larger reservoir tanks are recommended to reduce refilling of coolant during operation and allows for better temperature stability. At initial installation it is important to run unit in pump mode to circulate coolant prior to cooling to remove air bubbles.
Laird Thermal Systems Solution
The NRC400 Nextreme Performance Chiller is a premium thermoelectric-based chiller with high-performance Peltier coolers and heat exchanger technology. By utilizing next-generation thermoelectric coolers, it achieves 400 Watts of cooling capacity and a temperature control stability of ±0.05°C under steady state conditions.
Compared to previous models, the NRC400 offers OEMs a higher coefficient of performance (COP) and quieter operation. Solid-state thermoelectric technology reduces the number of moving parts, minimizing maintenance requirements throughout the life of the product.
Traditional compressor-based systems are often large and heavy. Modern cooling systems such as thermoelectric-based chillers are designed with portability in mind, which means that it can be used on multiple pieces of equipment around the laboratory.
The NRC400 features an intuitive easy-to-use LCD touchscreen display that allows users to easily control temperature setpoints and alarm features. The semi-closed system is equipped with a larger reservoir tank, requiring less refilling during operation and better temperature stability.
This product has been approved by UL for industrial lab use, reference UL 61010-1 and has CE marking. The NRC400 is RoHS compliant and environmentally friendly as no harmful HFC refrigerants are being used. It operates on a universal power supply, making it easy to source one part number for global use.
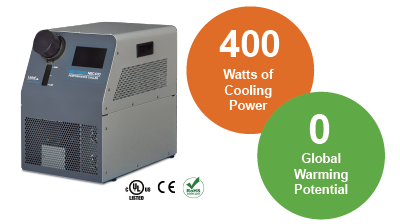
Conclusion
Microscope product innovations are primarily aimed at improving image resolution and reducing equipment and procedural costs. By developing better detectors, enhancing image reconstruction, increasing the efficiency of image acquisition and reducing the size of the equipment, analytical cameras will be able to deliver more accurate and detailed information to laboratory technicians. Recirculating chillers with thermoelectric coolers provide OEMs more sophisticated and precise cooling of analytical imaging systems to maximize image resolution, reduce maintenance, and lower the total cost of ownership.
More information on the NRC400 can be found on the Laird Thermal Systems website.
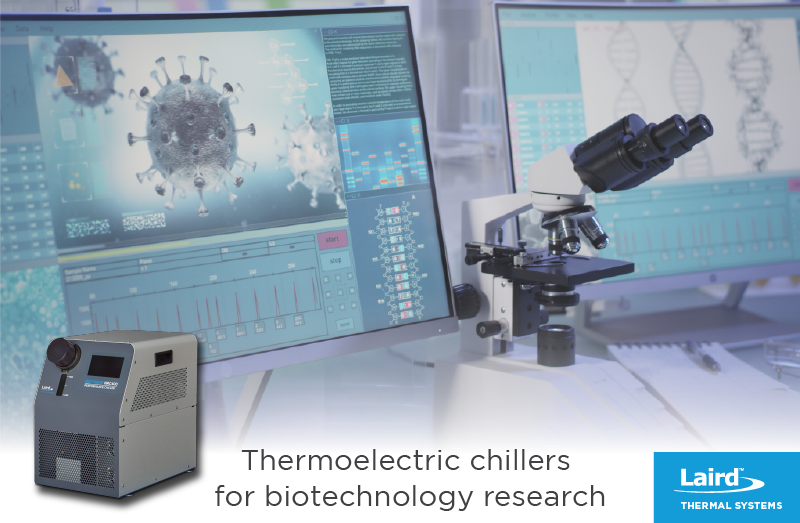