Introduction
Industrial lasers are used for a wide range of applications including cutting, welding, micro-machining, additive manufacturing and drilling. No matter the application, industrial laser systems generate a significant amount of heat. There are several different types of industrial laser technologies, ultimately distinguished by the power density of the laser and its use. For all laser technologies, OEMs seek advanced cooling of the power source and the laser optics. Temperature stability of these components is critical to ensuring the performance of the laser system and the satisfaction of their customers.
Chillers have been used to cool industrial laser systems for decades. However, new industry refrigerant restrictions and performance requirements have led industrial laser manufacturers to demand a more eco-friendly and maintenance-free chiller solution. The efficient and environmentally-friendly Nextreme™ Recirculating Chiller platform quietly cools temperature sensitive components below ambient temperature to ensure optimum laser performance, at a price point that enables competitive pricing of OEM bundled solutions.
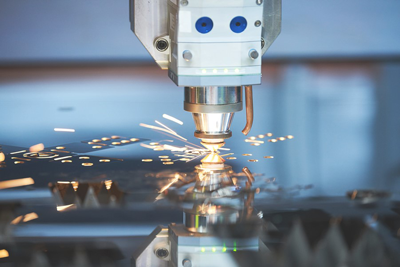
Industrial lasers used for cutting hard materials require a cooling solution to ensure stability of the laser beam.
Application Overview
Efficiently cooling lasers can be a significant challenge. For example, fiber lasers have better cooling characteristics over other media due to their specific arrangement, which enables them to spread the heat over a larger surface area. Ion lasers are characterized by the generation of extreme heat during lasing and the need for elaborate cooling measures. Carbon dioxide (CO2) lasers emit heat energy in the far-infrared and microwave region of the spectrum. To ensure proper, long-term performance of the laser, heat needs to be quickly and effectively dissipated by the cooling system.
Depending on system size and configuration, waste heat may be transferred by a coolant or directly to air. For laser systems that generate heat in excess of a few hundred watts, a liquid coolant solution is warranted. Coolant is circulated through a chiller or heat transfer system to pump heat away from sensitive laser components, maintaining a constant operating temperature.
Application Challenges
Many challenges exist in terms of the design, implementation and maintenance of liquid cooling solutions for industrial laser systems. If an industrial laser system goes down, it can shut down the entire manufacturing process. This can significantly impact production and incur large manufacturing costs. Therefore, robustness and maintenance-free operation of the chiller cooling system is critical to ensure maximum system uptime.
As previously mentioned, temperature stability is vital for both the industrial laser power supply and laser optics. Depending on the type of laser system and application, heat generated from the laser can be far more than kilowatts. For optimal performance, the laser optics typically require a stable operating temperature within 1°C of 20°C, while ambient temperature may fluctuate between 23°C to 35°C in a room temperature environment.
Miniaturization of industrial laser systems has led OEMs to pack more electronics into a smaller footprint. This increases the heat flux density and adds thermal load to the unit, making the industrial laser cooling solution even more important to the efficiency and performance of the laser power source and optics. To meet the required cooling capacity in a more compact form factor, the thermal management solution must have a high coefficient of performance (COP) for cooling well below ambient temperatures. Waste heat must be managed and dissipated efficiently in order to increase laser performance, while reducing power consumption and providing quieter operation (both lower noise and vibration).
Some coolant solutions feature cooling system pumps with greater pulsation. Pulsating pumps still offer the required system cooling, but create vibration within the cooling system. In laser systems, this has similar effects to thermal instability and results in a less-focused laser beam and lower-quality performance, which is critical in cutting and engraving applications. Industrial lasers are commonly used for cutting hard materials like steel. Basically, the laser beam melts through whatever material it is focused on. When cooled efficiently, the laser beam creates a finer, more precise cut or engraving. If the laser beam operates outside the optimum temperature range, it is not as focused and creates a rougher, less precise cut or engraving.
Many governments are requiring OEMs to phase out use of traditional ozone-depleting and high global-warming refrigerants. Older compressor-based systems utilize environmentally harmful HFC refrigerants including R134a and R404A. Modern compressor-based systems now use a variety of natural refrigerants: R744 (carbon dioxide), R717 (ammonia), R290 (propane), R600a (Iso-Butane), and R1270 (propylene). Although they have their own complications, including flammability, these natural refrigerants are significantly better for the environment.
Comparing Cooling Technologies
Traditionally used in industrial laser applications, compressor-based refrigeration systems offer a high coefficient of performance (COP). For example, if they are cooling a heat load of 3 kW, a standard compressor-based refrigeration system typically requires around 1 kW of energy to provide the proper cooling.
Compressor-based systems also tend to be smaller than alternative technologies like liquid-to-air heat exchangers, because they require less energy. In addition, liquid-to-air heat exchangers do not cool below ambient temperatures like compressor-based systems.
Central facility cooling systems used to cool the entire building have also been used for cooling industrial laser applications. However, these systems cannot guarantee a constant temperature and flow rate. It can also be difficult to satisfy all of the industrial cooling requirements with one large centrally controlled system.
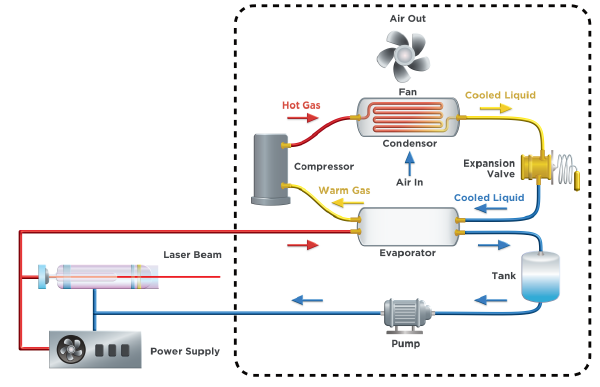
Compressor-based recirculating chillers offer efficient cooling for laser systems.
Laird Thermal Systems Solution
The Nextreme Value Chiller Series from Laird Thermal Systems offers reliable, cost-efficient temperature control. Based on the design for the Nextreme Performance Chiller Series, the Value line offers the same ease of use, high reliability, and low maintenance features as the Performance Series but at a lower cost through materials (brass instead of stainless steel), simpler components (single speed instead of variable speed compressor) and different control system (switches instead of sensors). This provides more competitive pricing to OEMs looking for a packaged solution with their instrument. Most importantly, the Nextreme Value Chillers can be configured and engineered to meet unique requirements for industrial applications.
The Nextreme Value Chiller Series uses high-performance, compressor-based technologies to cool equipment well below ambient temperatures and dissipate heat away from thermally sensitive equipment. The chillers from the value series offer a high coefficient of performance (COP) and can maintain a thermal set point with an accuracy of ±0.5°C in the supply coolant. Available in a footprint as small as 19.0 x 22.1 inches the Nextreme Value Chillers are smaller than most conventional cooling solutions.
The Nextreme Value Chiller Series is available in three standard models, 1200, 2400, and 4500 Watts. All these models can be configured to meet specific application requirements.
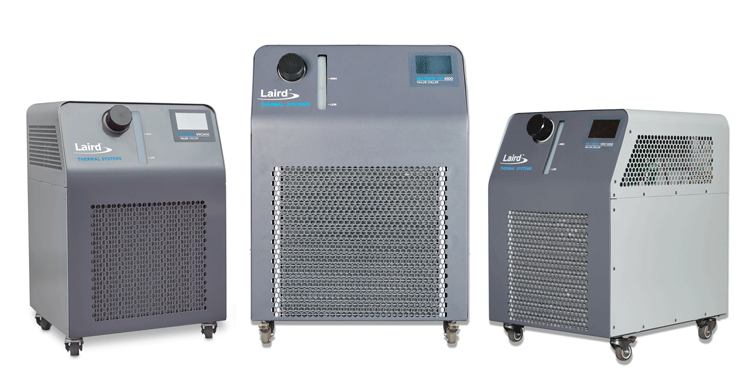
The Value Chiller products offer a lower cost of ownership and ease of use through:
- High reliability
- Pump technology with no-wear components
- Low fluid pulsation
- Capability of high pressure at rated flows
- Filtration and flow options
- Prevention of evaporative losses and bio-fouling
- Lower investment cost and added installation flexibility with the standard system
- Increased uptime
- Improved alarm condition detection
- Remote communication protocol for requesting data or send setpoints
- User-settable pressure limits to prevent equipment damage
The easy-to-use, LCD color touchscreen display comes standard and provides a simple user interface that communicates system status without the need for alarm codes or symbols. It allows the technician to control temperature setpoints, coolant type, pressure, and alarm settings while coolant level is easily monitored through the indicator window located on the front panel.
A semi-closed fluid system with pressure/vacuum reservoir cap prevents evaporative losses, the introduction of bacteria, and eliminates the need for additional hardware to prevent fluid drain-back. Other products on the market use an open/vented system that is simple to install and use but requires increased maintenance and monitoring of fluid levels and coolant quality. With the added functionality in the Value Chiller’s reservoir cap, less time is required to maintain system operation and uptime, and higher fluid quality level allows longer life of critical components like the pump, heat exchangers, and sensors.
Other standard features include optical fluid level-sensing with no moving parts; RS-232/Ethernet communications for integration into higher-level assembly control systems; and supply pressure sensing. Optional features include a hot-swappable, 5-micron water filter for filtering particulates from the coolant circuit and flow control valve and sensor to reduce and measure overall flow to the application (full flow continues through the chiller to maintain high heat transfer rates and temperature stability).
Using environmentally friendly R513A refrigerant, the Nextreme Value Chillers achieve similar performance with half the Global Warming Potential (GWP) compared to traditional hydrofluorocarbon (HFC) refrigerants. The chillers not only meet CE, REACH, and RoHS requirements but also UL61010-1 and IEC 61010-1 lab safety standards. While other chiller manufacturers require a different model for Europe and North America, Nextreme Value Chillers can be operated anywhere in the world. This allows OEMs to test equipment in one country before shipping to a different region. They also can carry less inventory as a single chiller can ship globally.
Most importantly, Laird Thermal Systems’ team works with OEMs to develop solutions that work best for their applications. Its design engineers can make modifications to the Value Chiller—such as supplying hose kits, modifying factory settings on the display, or changing out pump types—offering OEMs customized solutions with the cost and delivery times of off-the-shelf products. If the Value Chiller isn’t a fit for an OEM’s application, Laird Thermal Systems’ Thermal Wizard will help identify the right cooling solution that meets the application’s demands. Finally, Laird Thermal Systems supports OEM customers with high-mix products. Supply chain and production planning exceed industry standards with on-time delivery, so the OEM may carry low amounts of inventory and plan shipments on an as-needed basis with high confidence product will arrive on time.
The Value Chiller is a cost-effective, low-maintenance cooling solution that promises OEMs’ customers long-life component technology and system control that prevents failures, maximizing system uptime. This high reliability ensures end users experience fewer operational issues, increased throughput, and a better customer experience using OEMs’ equipment.
Conclusion
Properly cooling an analytic instrument like an electron microscope requires a sophisticated thermal management system. Modern compressor-based refrigeration systems are more advanced and efficient than previous versions. Compact chiller systems offer a higher coefficient of performance with maximum uptime and minimal power consumption compared to the application’s heat load. The versatile Nextreme Chiller provides quiet operation in a smaller and lighter package compared to previous models. The Nextreme recirculating chiller platform enables more focused and improved performance resulting in a precise image with better resolution.
More information on the Nextreme ValueChillers can be found by visiting
lairdthermal.com/nextreme-VRC1200
lairdthermal.com/nextreme-VRC2400
lairdthermal.com/nextreme-VRC4500
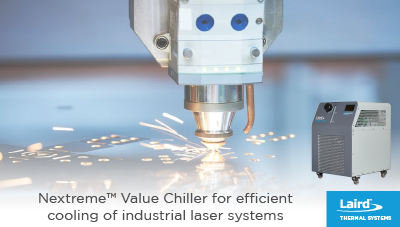