Introduction
Mass spectrometers measure the mass-to-charge ratio of molecules in a given sample. The technology helps forensic scientists and medical professionals, among others, identify a complex substance’s elements for applications in drug testing, food contamination detection, pesticide residue analysis, isotope ratio determination, protein identification and carbon dating. In medical labs, the equipment can diagnose nutritional and metabolism deficiencies, identify biomarkers and enzymes, and determine toxic levels of dangerous substances. In the forensics lab, mass spectrometers test for the presence of drugs and poisons. Due to the impact test results can have on those involved, it is critical the equipment perform reliably and accurately, while preserving the temperature-controlled lab environment required to conserve sample integrity throughout the process.
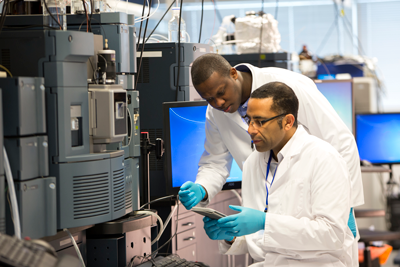
Mass spectrometry equipment needs to maintain precise temperature control in order to provide the most accurate test results.
To this end, compressor-based chillers with integrated temperature control offer mass spectrometer OEMs an advanced thermal management solution for maintaining the system’s optimum operating temperature. The ideal solution for such environments is an eco-friendly, efficient, and maintenance-free compressor-based chiller, such as the Nextreme™ Value Chiller, which quietly cools temperature-sensitive components below ambient temperature to help ensure accurate testing results.
Background
Put simply, a mass spectrometer breaks a molecular compound into a gas, then sorts the particles and identifies the fragments based on their molecular weight. The compound is injected into the spectrometer and heated under a vacuum until vaporized, creating an aerosol or plasma. The gas molecules then are broken into smaller bits known as “radical cations.” Some pieces of the molecule, however, remain whole; this “molecular ion peak” reveals the molecule’s weight, which the mass spectrometer uses to help determine the unknown component’s structure.
The radical cations that do break apart separate into neutral radicals and positively charged cations, and the latter are accelerated through the poles of a magnet and weighed by the mass spectrometer. The weight of the cation determines its rate of deflection by the magnet, with lighter particles deflected a lot and heavier particles deflected less. The smaller, lighter fragments will be “bent” by the spectrometer to hit the unit’s detector, while the heavier fragments crash into the walls and burn. By varying the magnetic field’s strength, scientists weigh the particles that hit the detector and compare them to the overall molecular ion peak, identifying the various elements contained in the sample.
Despite the wide variety of industries that utilize mass spectrometry—from photovoltaic to aerospace markets, from petrochemical to semiconductor to forensics industries—they all require equipment that is robust, easy-to-use, reliable, and, most of all, preserves the integrity of the samples as well as the mass spectrometer’s sensitive instrumentation. This is especially true of inductively coupled plasma mass spectrometry (ICP-MS), which uses plasma to ionize the sample. It is widely used to detect metals in liquid samples at low concentrations. This equipment is faster, more precise, and more sensitive than other mass spectrometry equipment, making the operating temperature—most often impacted by the plasma generator—a critical factor in performance.
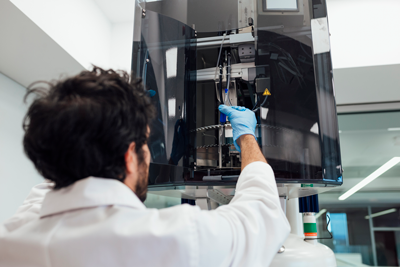
Inductively coupled plasma mass spectrometry is faster, more precise, and more sensitive than other mass spectrometry equipment, making the operating temperature a critical factor in performance.
Application Challenges
Designers face a number of thermal challenges when developing mass spectrometers.
Key spectrometer components depend on precise thermal management due to the heat-intensive nature of the process. The most critical of these is the plasma generator; the plasma must remain at an extremely high temperature to smash the molecules, yet the spectrometer must remain cool to ensure accurate measurement while maintaining the sample’s integrity.
Additionally, thermal challenges include overcoming the noise often generated by fans, airflow, and motors. Laboratory OEMs require thermal management solutions with low noise operation to create quiet environments for precise, contemplative work.
In addition to meeting thermal control requirements, cooling solutions must be compact and able to fit in spaces above or below the benchtop spectrometers. Mass spectrometer OEMs continue to decrease device size while increasing functionality. As a result, more electronics are packaged into smaller housings, increasing the heat flux density and thermal challenges. This waste heat must be managed and dissipated efficiently—without generating excess vibrations or noise. Some liquid pump chiller models, for example, cause vibration due to higher pulsations in the fluid lines. This is the case with rotary vane or some centrifugal pumps. Turbine pumps, on the other hand, have significantly less pulsation, which help improves operation of the spectrometer.
Finally, many countries enforce strict environmental regulations that analytic tools like mass spectrometers must meet. For example, laboratories that qualify for Leadership in Energy and Environmental Design (LEED) certifications must prove efforts to go green. In addition, labs in most countries are now required by law to use cooling equipment with refrigerants that are environmentally safe. Europe’s RoHS (Reduction of Hazardous Substances) and REACH (Registration, Evaluation, Authorization and Restriction of Chemicals) regulations also impact the cooling system design. A mass spectrometer’s cooling system also must meet UL61010-1 or IEC 61010-1 lab safety standards, which ensures safety of the operators and includes specifications for electromagnetic compatibility and electromagnetic emissions to ensure all laboratory equipment can operate in the same room without interference.
Advanced compressor-based recirculating liquid chillers are a smaller and more portable solution, offering precise temperature control for analytical equipment and delivering improved cost, size, noise, and environmental impact savings.
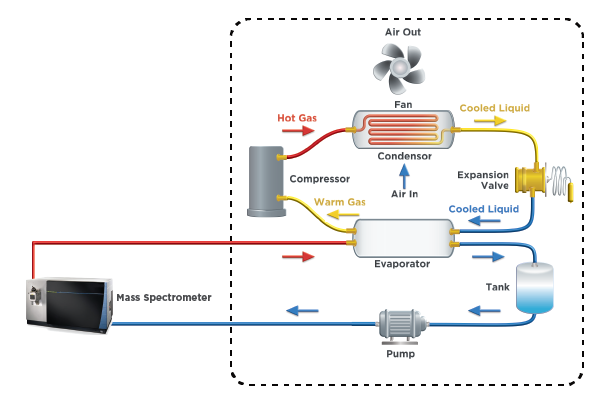
Compressor-based refrigeration systems control the temperature of water or water with glycol (antifreeze) in a liquid circuit, which is an efficient method of cooling mass spectrometers. The coolant is recirculated by using a highly reliable pump. Heat from the coolant is absorbed by a durable, compressor-based system and dissipated into the ambient environment.
Laird Thermal Systems Solution
The Nextreme Value Chiller Series from Laird Thermal Systems offers reliable, cost-efficient temperature control. Based on the design for the Nextreme Performance Chiller Series, the Value line offers the same ease of use, high reliability, and low maintenance features as the Performance Series but at a lower cost through materials (brass instead of stainless steel), simpler components (single speed instead of variable speed compressor) and different control system (switches instead of sensors). This provides more competitive pricing to OEMs looking for a packaged solution with their instrument. Most importantly, the Nextreme Value Chillers can be configured and engineered to meet unique requirements for mass spectrometry applications.
The Nextreme Value Chiller Series uses high-performance, compressor-based technologies to cool equipment well below ambient temperatures and dissipate heat away from thermally sensitive equipment. The chillers from the value series offer a high coefficient of performance (COP) and can maintain a thermal set point with an accuracy of ±0.5°C in the supply coolant. Available in a footprint as small as 19.0 x 22.1 inches the Nextreme Value Chillers are smaller than most conventional cooling solutions.
The Nextreme Value Chiller Series is available in three standard models, 1200, 2400, and 4500 Watts. All these models can be configured to meet specific application requirements.
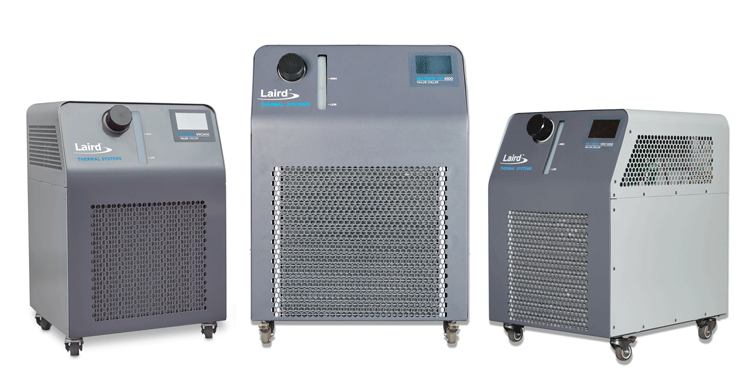
The Value Chiller products offer a lower cost of ownership and ease of use through:
- High reliability
- Pump technology with no-wear components
- Low fluid pulsation
- Capability of high pressure at rated flows
- Filtration and flow options
- Prevention of evaporative losses and bio-fouling
- Lower investment cost and added installation flexibility with the standard system
- Increased uptime
- Improved alarm condition detection
- Remote communication protocol for requesting data or send setpoints
- User-settable pressure limits to prevent equipment damage
The easy-to-use, LCD color touchscreen display comes standard and provides a simple user interface that communicates system status without the need for alarm codes or symbols. It allows the technician to control temperature setpoints, coolant type, pressure, and alarm settings while coolant level is easily monitored through the indicator window located on the front panel.
A semi-closed fluid system with pressure/vacuum reservoir cap prevents evaporative losses, the introduction of bacteria, and eliminates the need for additional hardware to prevent fluid drain-back. Other products on the market use an open/vented system that is simple to install and use but requires increased maintenance and monitoring of fluid levels and coolant quality. With the added functionality in the Value Chiller’s reservoir cap, less time is required to maintain system operation and uptime, and higher fluid quality level allows longer life of critical components like the pump, heat exchangers, and sensors.
Other standard features include optical fluid level-sensing with no moving parts; RS-232/Ethernet communications for integration into higher-level assembly control systems; and supply pressure sensing. Optional features include a hot-swappable, 5-micron water filter for filtering particulates from the coolant circuit and flow control valve and sensor to reduce and measure overall flow to the application (full flow continues through the chiller to maintain high heat transfer rates and temperature stability).
Using environmentally friendly R513A refrigerant, the Nextreme Value Chillers achieve similar performance with half the Global Warming Potential (GWP) compared to traditional hydrofluorocarbon (HFC) refrigerants. The chillers not only meet CE, REACH, and RoHS requirements but also UL61010-1 and IEC 61010-1 lab safety standards. While other chiller manufacturers require a different model for Europe and North America, Nextreme Value Chillers can be operated anywhere in the world. This allows OEMs to test equipment in one country before shipping to a different region. They also can carry less inventory as a single chiller can ship globally.
Most importantly, Laird Thermal Systems’ team works with OEMs to develop solutions that work best for their applications. Its design engineers can make modifications to the Value Chiller—such as supplying hose kits, modifying factory settings on the display, or changing out pump types—offering OEMs customized solutions with the cost and delivery times of off-the-shelf products. If the Value Chiller isn’t a fit for an OEM’s application, Laird Thermal Systems’ Thermal Wizard will help identify the right cooling solution that meets the application’s demands. Finally, Laird Thermal Systems supports OEM customers with high-mix products. Supply chain and production planning exceed industry standards with on-time delivery, so the OEM may carry low amounts of inventory and plan shipments on an as-needed basis with high confidence product will arrive on time.
The Value Chiller is a cost-effective, low-maintenance cooling solution that promises OEMs’ customers long-life component technology and system control that prevents failures, maximizing system uptime. This high reliability ensures end users experience fewer operational issues, increased throughput, and a better customer experience using OEMs’ equipment.
Conclusion
Properly cooling an analytic instrument like an electron microscope requires a sophisticated thermal management system. Modern compressor-based refrigeration systems are more advanced and efficient than previous versions. Compact chiller systems offer a higher coefficient of performance with maximum uptime and minimal power consumption compared to the application’s heat load. The versatile Nextreme Chiller provides quiet operation in a smaller and lighter package compared to previous models. The Nextreme recirculating chiller platform enables more focused and improved performance resulting in a precise image with better resolution.
More information on the Nextreme ValueChillers can be found by visiting
lairdthermal.com/nextreme-VRC1200
lairdthermal.com/nextreme-VRC2400
lairdthermal.com/nextreme-VRC4500
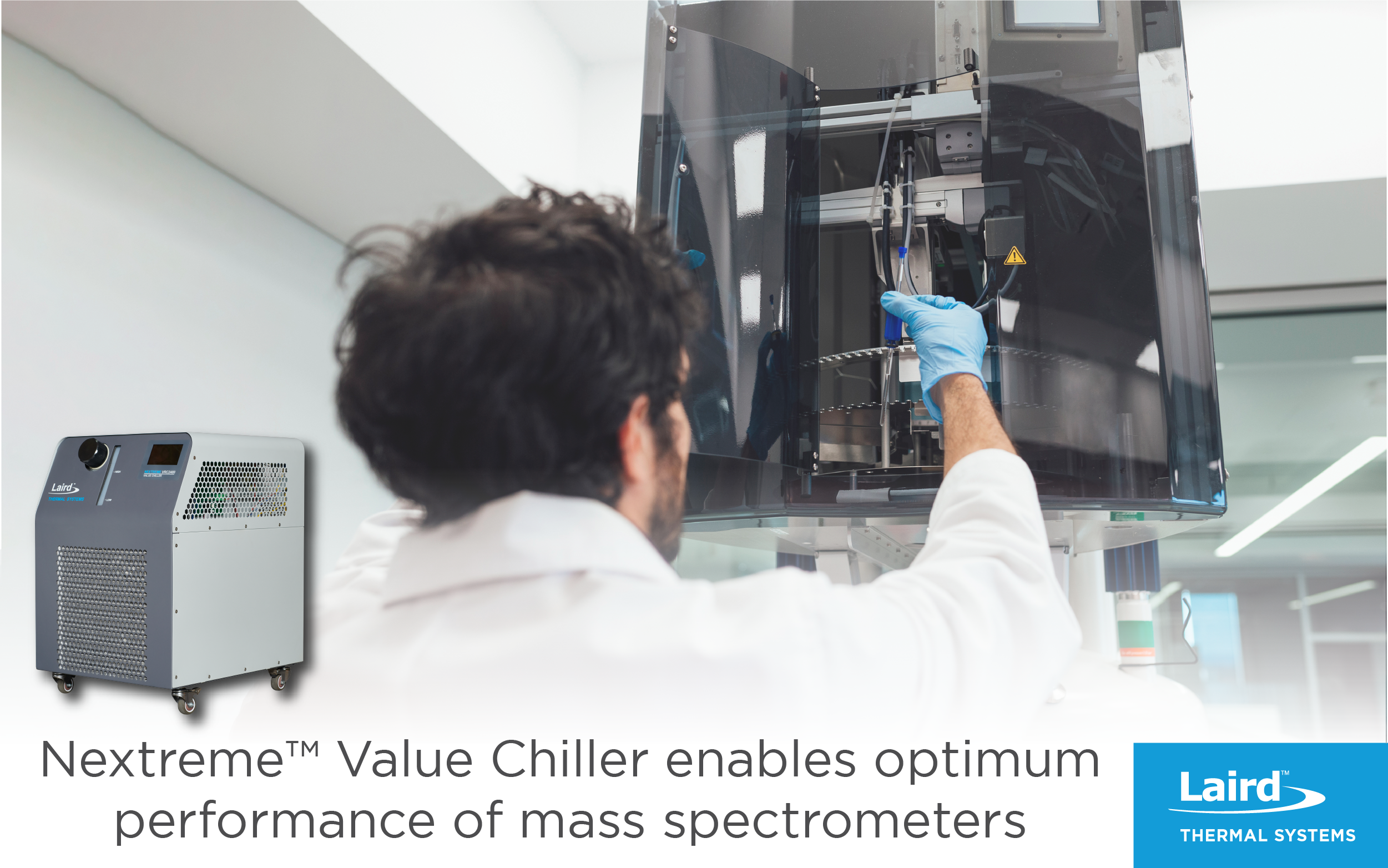