Introduction
Centrifugation is a process that separates mixtures through centrifugal force. Centrifuges are commonly used in food processing and medical research for protein, genetic and cellular analysis. In medical laboratory settings, centrifugation involves spinning medical samples at a fast rate to filter or concentrate substances based on differing densities. Dense components migrate away from the center axis, while less dense components migrate towards the axis.
To meet a variety of sample volume, g-force and revolutions per minute (RPM) requirements, centrifuges are offered in a variety of models. These include sophisticated ultracentrifuges, high-speed centrifuges, large capacity centrifuges and smaller benchtop centrifuges. In terms of thermal management, there are two types of laboratory centrifuges. Standard ventilated centrifuges are capable of managing the temperature in the bowl and their effectiveness depends on the design of centrifuge. High-end refrigerated centrifuges that offer thermal management for samples require temperature control beyond ambient conditions. Many sample types require precision temperature control inside the centrifuge chamber. This is especially true for sensitive live cells and proteins that must be stored and tested at specific consistent temperatures to ensure proper reaction and viability.
To ensure precise temperature control for laboratory centrifuge applications, active Peltier coolers and assemblies are the ideal thermal management solution. Compared to compressor based technologies, Peltier cooling is more efficient, cost-effective and reliable. In addition, government restrictions of traditional and natural refrigerants, fundamental to compressor-based systems, are affecting past, present and future thermal management system designs. Refrigerant-free Peltier cooling offers a more desirable, future-proof solution for temperature control in centrifuge applications.
Thermal Challenges
Laboratory centrifuge manufacturers face several thermal management design challenges such as temperature stability, space constraints, noise levels, vibration, reduced power consumption and refrigerant restrictions.
Depending on the type of sample, a centrifuge tub typically must maintain a precise temperature between 0°C and 40°C throughout the centrifuge process while working in ambient temperatures of 23°C to 30°C. For example, human tissue samples must be kept at the mammalian body temperature of 37°C. Temperature changes by as little as 6°C can significantly impact cell health and render the centrifuge process worthless.
Centrifuge heat load cooling requirements can range from less than 30 to more than 150 Watts depending on the centrifuge type and size. Cooling solutions must be able to efficiently remove the required heat load with a high coefficient of performance to minimize power consumption.
Miniaturization of all lab equipment, including centrifuges, to free up lab space has led engineers to pack more electronics into a smaller footprint. More electronics in a reduced space increases device functionality but also increase the heat flux density. Tight space constraints require an efficient and effective heat exchanger with advanced thermal control capability. The cooling unit needs to feature a compact form factor to maximize the chamber volume of a centrifuge.
Because technicians use medical centrifuges in a laboratory setting, operating noise levels are a significant design concern. From the rotor to the thermal management solution, centrifuge systems need to offer quiet operation as to not interfere with lab operation.
Lastly, many governments are requiring OEM’s to phase out use of hazardous refrigerants. Older compressor-based systems utilize environmentally harmful HFC refrigerants including R134a and R404A. Modern compressor-based systems now use a variety of natural refrigerants: R744 (carbon dioxide), R717 (ammonia), R290 (propane), R600a (isobutene), and R1270 (propylene). However, natural refrigerants pose different design challenges such as increased pressure, high toxicity, flammability, asphyxiation and relatively poor performance. The flammable nature of some natural refrigerants makes them hazardous to transport. As a result, centrifuge manufacturers are looking for alternative technologies such as Peltier cooling.
Thermoelectric Coolers
Thermoelectric coolers are active solid-state heat pumps that operate via the Peltier effect. These thermoelectric coolers, often referred to as Peltier coolers move heat efficiently to protect samples/fluids and ensure proper function of the centrifuge. Thermoelectric coolers are designed with size, efficiency, cost and continuous reliable operation in mind to enable centrifuge OEMs to meet thermal design challenges.
Thermoelectric coolers feature a low thermal resistance to increase the heat-pumping capacity, operate at a higher coefficient of performance (COP), and reduce power consumption. When DC current flows through the Thermoelectric cooler, one side gets hot, while the opposite side gets cold. If the direction of current flow is reversed, then the two sides reverse their function. Manufacturers of thermoelectric coolers define two specifications: ΔTMax and QcMax. ΔTMax is the maximum temperature differential with no heat flow (Qc = 0). QcMax is the maximum heat flow when no temperature difference exists (ΔT = 0). For most single-stage thermoelectric coolers ΔTMax is typically near 70°C. As soon as heat (Qc) is required to move through the thermal interface, the usable ΔT value drops until the QcMax value is reached at ΔT = 0. In addition to the trade-off between ΔT and Qc, much of this temperature differential can be lost through thermal resistances on both the hot and cold side of the thermoelectric cooler. Thermal interface material and the choice of heat sinks represent the greatest design challenges. If increased cooling capacity (Qc) is demanded, then either lower thermal resistance heat sinks or more thermoelectric coolers are required. This can be done by wiring thermoelectric coolers in series or parallel to accommodate 12 or 24 VDC. Real-world operation of thermoelectric coolers involves the combination of ΔT and Qc to meet centrifuge cooling requirements for temperature stabilization.
Laird Thermal Systems’ Ceramic Plate (CP) Series is a rugged, compact thermoelectric cooler designed for higher current and large heat-pumping applications like benchtop and high-speed centrifuges. Placed underneath the centrifuge tub to cool from the bottom, the CP Series direct-to-air configuration offers a maximum cooling power of up to 125 Watts with a temperature difference (ΔT) of 67°C in a small form factor of 62 mm x 62 mm x 4.6 mm or smaller. The CP Series is available in a wide range of heat pumping capacities, geometric shapes, and input power ranges to meet centrifuge requirements.
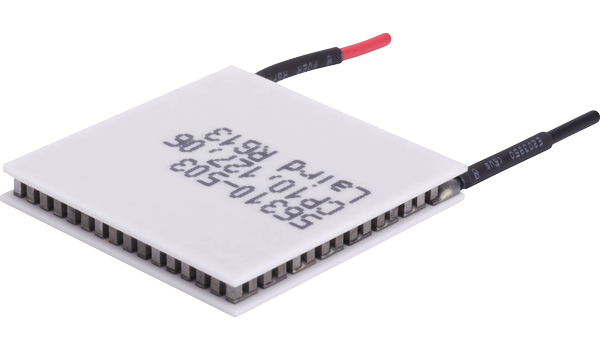
CP Series Thermoelectric Cooler
With no moving parts, choosing solid-state thermoelectric coolers increase reliability and durability in high-vibration applications like centrifuges. These active cooling devices also contribute to reduced operational noise levels. Overall, Thermoelectric coolers significantly decrease maintenance, operation and total ownership costs.
Thermoelectric Cooler Assemblies with Temperature Controllers
Peltier cooling assemblies, or thermoelectric cooler assemblies, utilize thermoelectric coolers to offer a higher cooling capacity spectrum, ranging from approximately 10 to 250 Watts. Thermoelectric cooler assemblies can cool by removing heat from control sources through forced convection (air or liquid), and conduction. Ultracentrifuges and high-speed centrifuges typically require a thermoelectric assembly cooling solution. The Tunnel Series thermoelectric cooler assembly offers cooling capacities up to 100 Watts with higher efficiencies that run quieter, while the SuperCool X Series thermoelectric cooler assembly offers cooling capacities of more than 200 Watts in a smaller form factor.
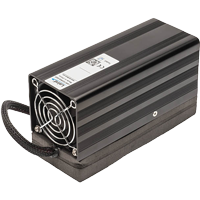
Tunnel Series

SuperCool X Series
When used with a temperature control unit, Peltier cooling assemblies offer several advantages over other cooling technologies including cooling below ambient temperatures, fast ramp rates, precise temperature control, accurate to within ±0.01˚C under steady-state conditions, and low noise. These temperature control systems are also environmentally friendly, as they do not utilize refrigerants to achieve accurate temperature control inside the centrifuge.
The use of a closed-loop temperature controller with a Peltier cooler or assembly delivers a highly responsive and accurate thermal control system. A temperature controller takes feedback from a temperature sensor to vary the output of the power supply to control the temperature inside a centrifuge tub. Thermal controllers can be customized to a variety of control options to deliver energy savings and trip alarms. I/O contacts are available for fans, thermoelectric coolers, alarm/status LEDs, thermistors, fan tachometer sensors and an overheat thermostat.
The Laird Thermal Systems’ SR-54 Series temperature controller offers temperature control to within +/- 0.5 °C when combined with the SuperCool X or Tunnel Series thermoelectric cooler assemblies. The SR-54 temperature controller also monitors voltages, temperatures and fan tachometers to trigger an alarm to identify a problematic fan, thermoelectric cooler, over-temperature thermostat and temperature sensor failure — all of which are critical to maximizing centrifuge uptime. The controller requires minimal programming and can be easily configured with a thermoelectric cooler assembly or system enclosure. The controller also lowers operational noise, as fan speeds can be lowered once the specified temperature has been reached.
Another option is the PR-59 temperature controller with power regulation that is selectable and user-configurable for PID (proportional-integral-derivative), thermostat ON/OFF, or POWER, protecting equipment and optimizing performance. The PR-59 programmable microcontroller delivers control stability to within ±0.05°C of the set point in both heating and cooling modes. By connecting to a PC with associated software, temperature set points and other parameters can be selected.
Conclusion
High-end refrigerated centrifuges require a thermal management system that delivers precise temperature control during operation. The use of active Peltier cooling modules or assemblies is ideal for laboratory centrifuge applications. Thermoelectric coolers and assemblies offer compact, efficient thermal solutions, giving stable and reliable performance at a lower total cost-of-ownership. Laird Thermal Systems has decades of experience in providing cooling solutions for refrigerated centrifuges, as well as exceptional customer support. With an extensive product breadth and diverse portfolio, Laird Thermal Systems offers advanced thermoelectric coolers, thermoelectric cooler assemblies and temperature controllers.
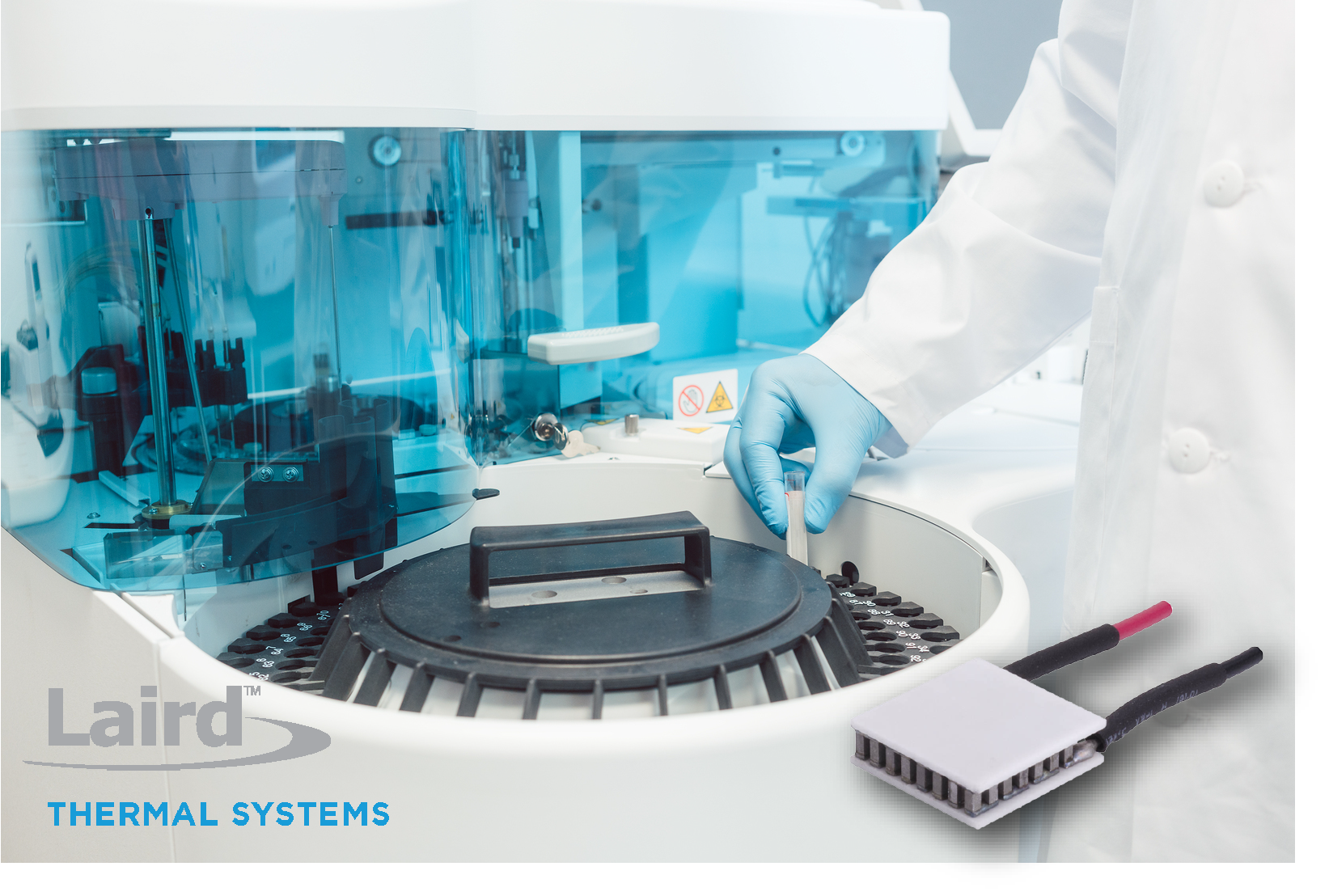